Material Specific Tooling in CNC Machining
The importance of selecting the right tool for a machining operation is already established. As a professional machinist, tool selection might pose a dilemma, especially when dealing with first-time projects or jobs that are relatively complex. Machining may be done with generic, custom or special-purpose tools. The latter, is where material-specific tooling comes in.
Material-specific tooling is the process of running a machining operation with the use of a tool that is specially selected and deemed appropriate for the job. These tools are often more expensive than conventional machining tools. The benefits of using material-specific tooling, in the long run, outweigh the costs. However, there are a number of factors to consider before concluding on material-specific tooling. From the material removal rate to cost and purpose, let’s take a look at the concept of material specific tooling in CNC machining.
Material-Specific Tooling – What, why and when?
As we have briefly described above, material-specific tooling involves the use of a tool designed for a special purpose production. It essentially takes factors like the material to be machined, the quantity of units and the level of precision to be achieved into consideration to come up with the perfect tool for the job operation.
Material-specific tooling is most optimal when dealing with a large production batch of items made from similar material. If flexibility is a concern to your business, material-specific tooling may not be an economic option. However, when dealing with units above 1000 parts, material-specific tooling will help to deliver better accuracy, high-quality part finish and optimal performance on your operation. Also, because the tooling is material-specific, the lifespan of the tool can be expected to be considerably longer.
Generally, investing in material specific tooling is dependent on the type of business you engage. If you often deal with similar materials, material-specific tooling pays off. If your business deals with multiple materials during its day-to-day operations, a regular end mill of different types should be good enough.
Advantages of Material-Specific Tooling
Material-specific tooling comes with a number of pros. Below are the most significant benefits of taking a material-specific tooling approach to machining:
• Precise plastic tooling process geometry
This is the foremost advantage of material-specific tooling.
Because this process essentially involves creating end-parts for specific purposes, machinists will get to benefit from the use of tools with the exact, required geometry for the workpiece to be manufactured.
The special geometry in the tool created allows the machinists to take advantage of certain special parameters like rake, relief design, cutting edge and balance to deliver cuts that will quickly breakdown the workpiece, enhance heat dissipation and more to help deliver the perfect end-part.
The downside to material-specific tooling and exact tooling geometry may however arise in the lack of flexibility of the tool as it is only built for one specific purpose.
• Optimal machining rates
Do more with increased feed rates, speed and turnaround times without the risk of damaging your machine or encountering workpiece damage. With material-specific tooling, the chances of tool deflection and breakage at high speeds is also significantly reduced. The consequences of this is improved part finish, axial depths of cut, radial depths of cut, and consequently, enhanced material removal rates.
• Enhanced material removal rates
Material removal rates (MRR) refers to the rate at which a tool can remove material from a workpiece. In order to run at optimal capability, the material removal rate of a tool should be perfect for the workpiece being drilled/milled. MRR is also the most relevant metric that defines the productivity of any workshop.
When material-specific tooling is employed, machinist will benefit from producing parts faster and more optimally from a workpiece because the tooling allows for a generally more aggressive production process. Here, materials are machined faster, more accurately and material waste is significantly minimized.
• Material coating and Improved tool lifespan
Another crucial merit of material-specific tooling is the ability to select and use the best possible coating solution that matches the properties of the material to be machined. In CNC machining, tool coating help to keep the friction at bay, enhances tool performance by increasing mobility, lubricity and speed.
The opportunity of material-specific tooling means that you can custom manufacture a tool that will enhance your heat-dissipation, machining fluidity and run at optimal performance in conditions that other generic tools may fail at in the absence of special coatings. Because material-specific tooling are bespoke to match their end-use, one can also expect a longer lifespan as your tool is built for optimal performance in the conditions it is being used.
• Longer term cost savings
Although the initial costs of making a material-specific tool can be high side, the overall effect in the long run is significant cost savings. When making a custom tool for special purposes, one can expect to spend more on the material, coating and other tooling specifics. This cost is understandably higher than the cost of obtaining regular end mill and drill tools.
When factors like tool damage, wear, breakage and dullness are put into consideration, material-specific tools will deliver longer term savings over conventional tools. This cost savings can be up to $2000 over a production range of 1000 end parts.
FirstPart CNC Machining in China
FirstPart is one of China’s leading manufacturing hub for Additive, CNC and Conventional manufacturing techniques. We boast of excellent in-house capacity, labor force and logistics while delivering exceptional value for money. Our array of services include CNC machining, 3D printing, Rapid Tooling, Die casting, Rapid prototyping, Plastic Injection Molding, Urethane Casting, Aluminum Extrusion, Post-machining/Finishing services and much more.
As we understand the start-up challenges that is faced by new businesses, engineers and product developers, we offer both mass production, bridge tooling and low-volume prototyping/manufacturing with no minimum order quantities. Our services are flexible, saleable and innovative, with a team of engineers and design experts available to support you through your entire product development cycle.
Click here to get in touch with us and receive a free quote and project review. To contact us via phone or email, or for all other inquiries, please click here.
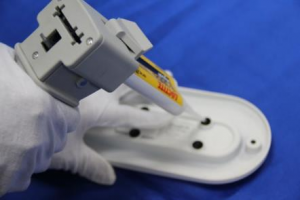