PLASTIC INJECTION MOLDING SERVICE
- 100+ Materials & Finishing For Choosen
- 1-10,000 Flexible MOQ
- T1 Sample As Quick As 7 Days
- Prototyping & Production Mold-making
Certifications: IATF 16949:2016, ISO 9001:2015
Top 10 Choice for Injection Molding Services
First Part specializes in the use of rapid prototyping and On-demand manufacturing techniques to produce high-end plastic injection molded parts and mold tools. Our plastic injection molding process is capable of making custom prototypes and end-use parts in as quick as 7 days. At First Part, cost-efficiency is optimized by using aluminum mold tooling that can reproduce thousands of parts and accelerate your product development cycle.
We stock over 100 plastic resin materials to choose from and complement molded part with an array of finishes. To get started, Click here to upload your project design information and receive an instant quote.
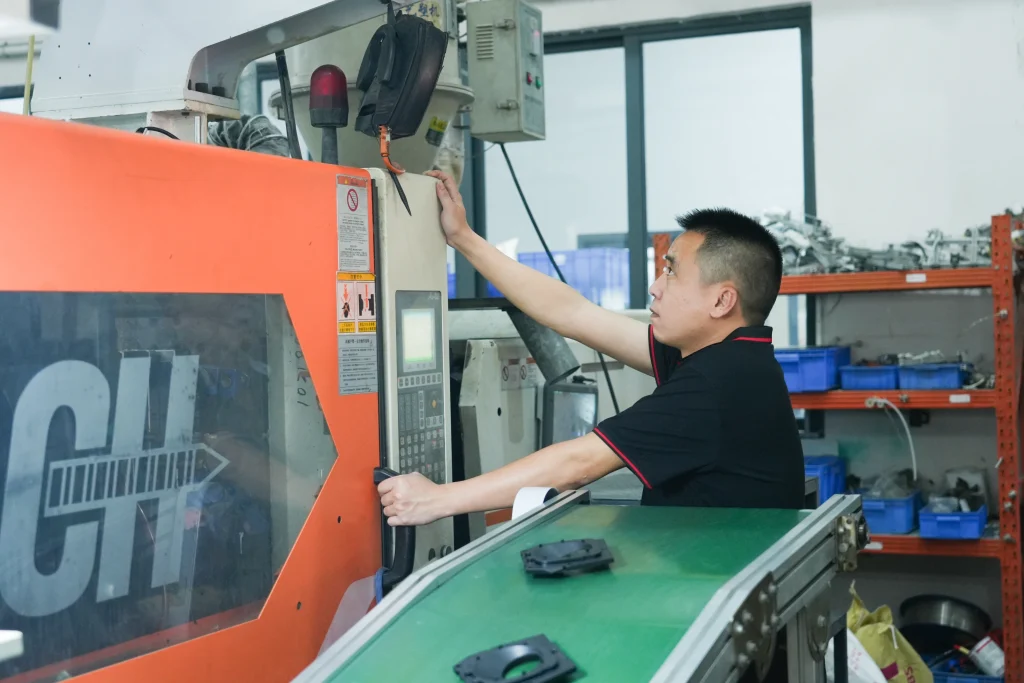
Advantages of Injection Molding Service
First Part core competitiveness
10+ Years Industry Experience
Expertise, high quality manufacturing;
Industry application: automotive, medical, electronic, digital consumer etc.
Custom Design Capability
Offering free design service.
Quick DFM, complex mold design available.
Cost-effectiveness
Affordable prototyping & production tooling;
Free mold maintenance;
Re-order discount.
Efficiency & Quality
T1 sample within 7 days;
Strict QC policy;
Quality steel tooling
Flexible Materials & Finishes
Over 100 materials + custom materials for choosen;
Multi finishes to your needs.
Responsive Customer Service
7*24 customer service;
Quick reply within 24hrs
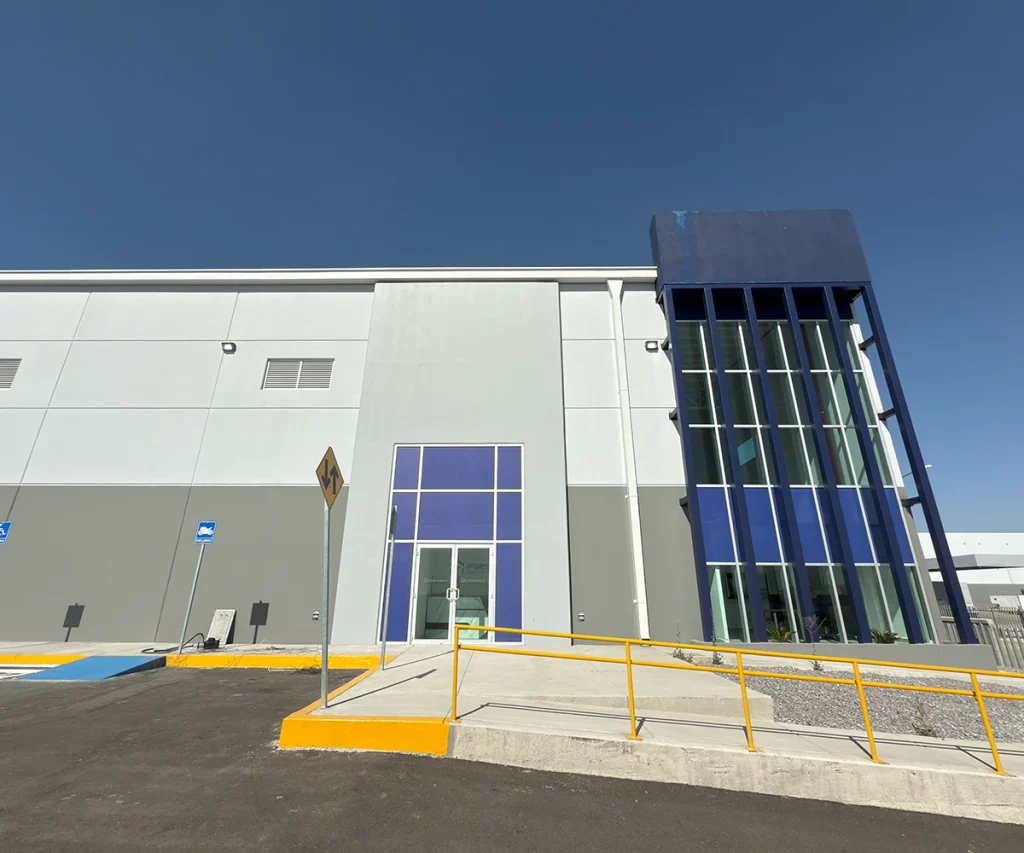
Dual-Base Advantage: Global Reach, Local Precision
At First Part, our China & Mexico manufacturing hubs are strategically positioned to serve your global needs while minimizing tariff impacts:
Your Strategic Advantages
- Leverage our dual-base manufacturing model to bypass punitive tariffs, strategically aligning production locations with optimal trade agreements to ensure significant reductions in total landed costs.
- We fully manage end-to-end regulatory processes, including origin certification and customs classification, eliminating hidden fees and ensuring adherence to international trade protocols.
- Our cross-continental infrastructure guarantees uninterrupted production, with backup facilities capable of activating full operational capacity within 72 hours to counter regional disruptions
Our Injection Molding Capabilities
In First Part, experienced team for plastic injection molding service. Our injection molding and rapid processing services perfectly match. We can efficiently and accurately complete custom parts.At the same time, our injection molding services can suit the application requirements of any industry.
Mold Making
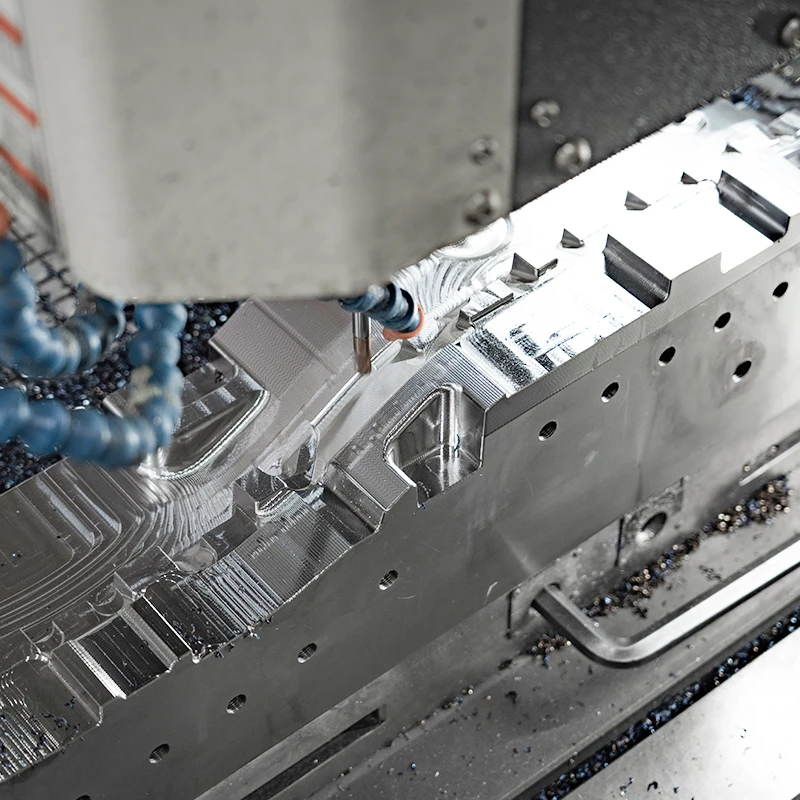
Our competence and capabilities are centered around integrating digital manufacturing technologies with conventional manufacturing processes. This is why we can use high-quality 3D designs to rapidly manufacture high-precision mold tools in a matter of days.
We offer rapid tooling, mold making, and die manufacturing for both low-volume production, mass production, and prototyping. Our expertise includes steel, and aluminum tooling, and mold maintenance, redesign services.
Plastic Injection Molding
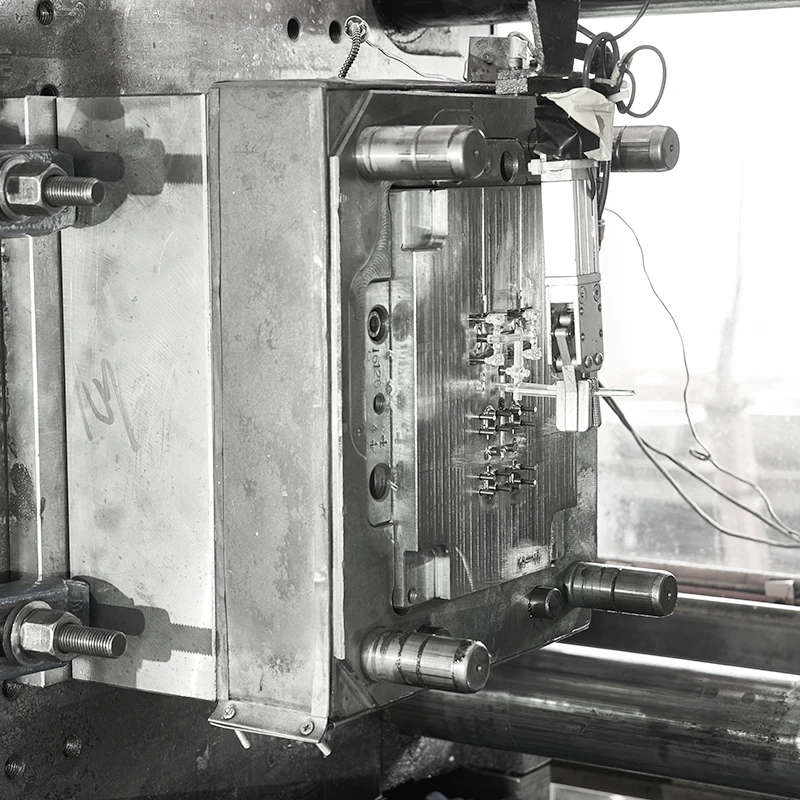
First Part uses high-quality thermoplastic materials to deliver top-grade plastic injection molded parts in as quick as 7 days. From our instant quoting service to design evaluation, toolmaking, die, and mold production, and finally injection molding, we stay true to our promise of quality.
Our entire injection molding capabilities include insert molding, mold making, rapid tooling, and overmolding.
Overmolding
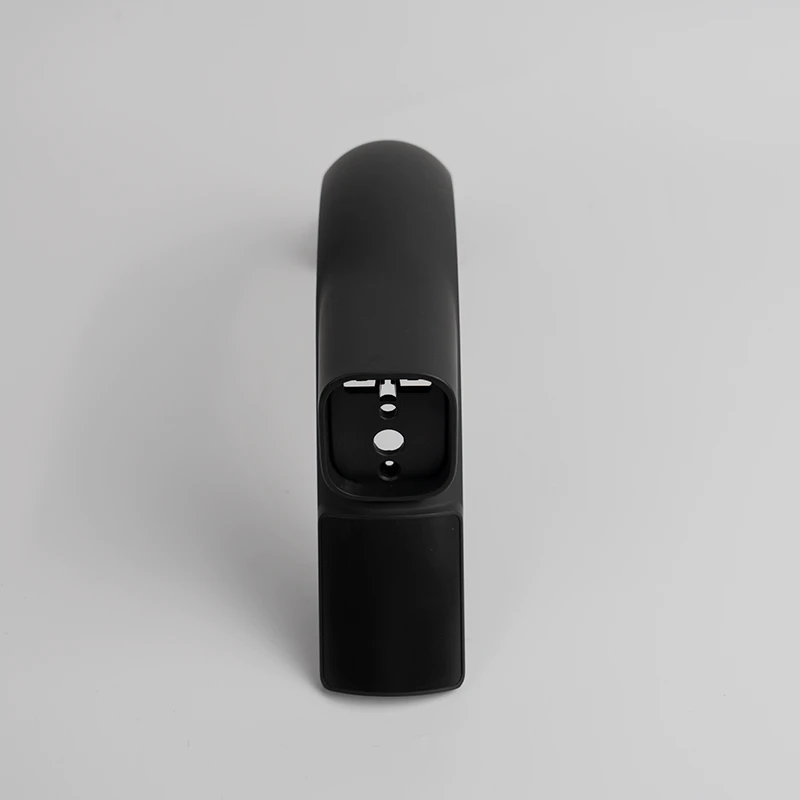
Overmolding is an injection molding operation that is used to make a single part from multiple materials. At First Part, we can mold a thermoplastic material into a second material to leverage certain performance and characteristic attributes of the materials to complement functionality. An example is the solid plastic body and rubberized handles of toothbrushes. Overmolding is very effective for creating composite parts, costing lesser than other production techniques that require assembly of separate components.
Insert Molding
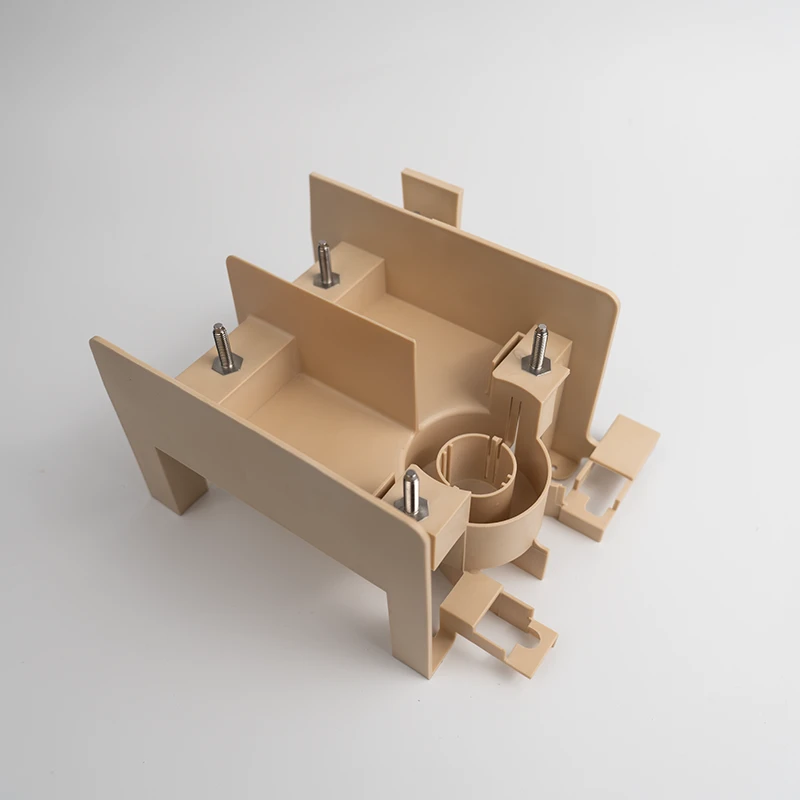
Insert molding is one of First Part’s injection molding capabilities, enabling us to create or integrate plastic fragments and components (inserts) to the pre-fabricated metal part. Through our expertise in cross-technology fabrication, we can use sheet metal and CNC machining to make units of your metal part and employ insert molding to introduce plastic parts. Insert molding can be used in making tools that are sharp and require a grip. Examples include scalpels, fasteners, bushings, or clips.
Injection Molding Applications
First Part Injection Molding Operations can be applied in:
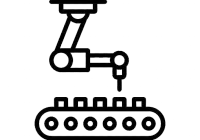
· High-functional end-part production
Injection molding is widely used in making functional end-use parts that will replace metal parts in most components. Choose from materials to finishes to make high-quality parts that are of high strength and less weight than metal counterparts.
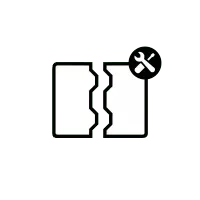
· Rapid tooling/Mold making
We can use our optimized injection molding process to manufacture molds, tooling (cores and cavities), and dies for use in making any range of budget, volume, and production times.
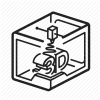
· Rapid Prototyping
Take advantage of low-cost tooling options to allow you to make highly-functional parts that are suitable for functionality testing. Even when tooling with aluminum molds, our injection molded parts are almost certain to outperform 3D printed or CNC machined parts from the same material. A low-cost mold can be made in a shorter window, and depending on size and geometry, it could be used in making many volumes. (up to thousands of prototypes)
How It Works: 4-Step Ordering
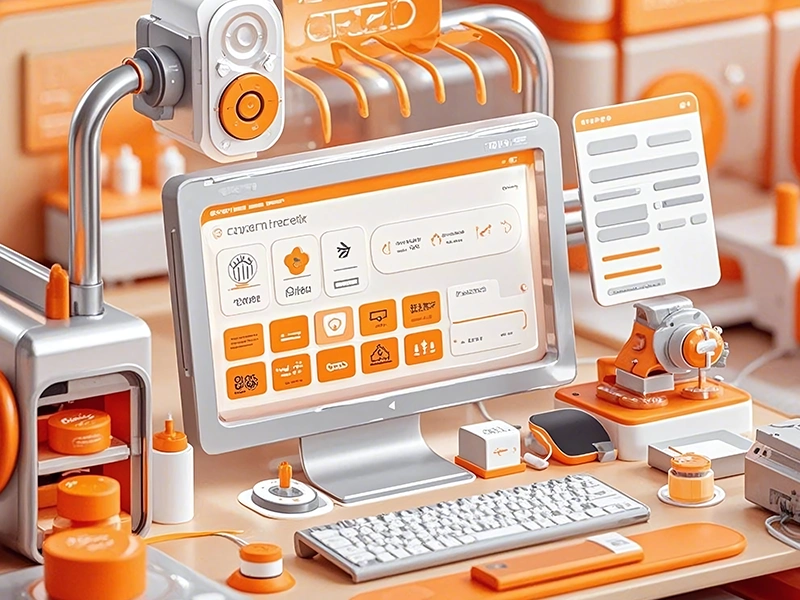
Step 1: Upload Your Design
Upload your 3D design file with online form
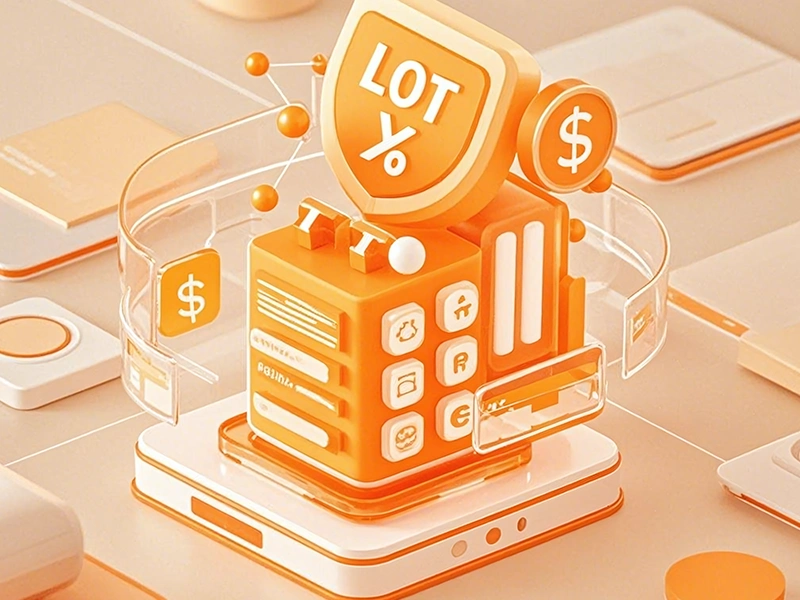
Step 2: Get Instant Quote & Free DFM
Quick quote and expert DFM as fast as 1 day
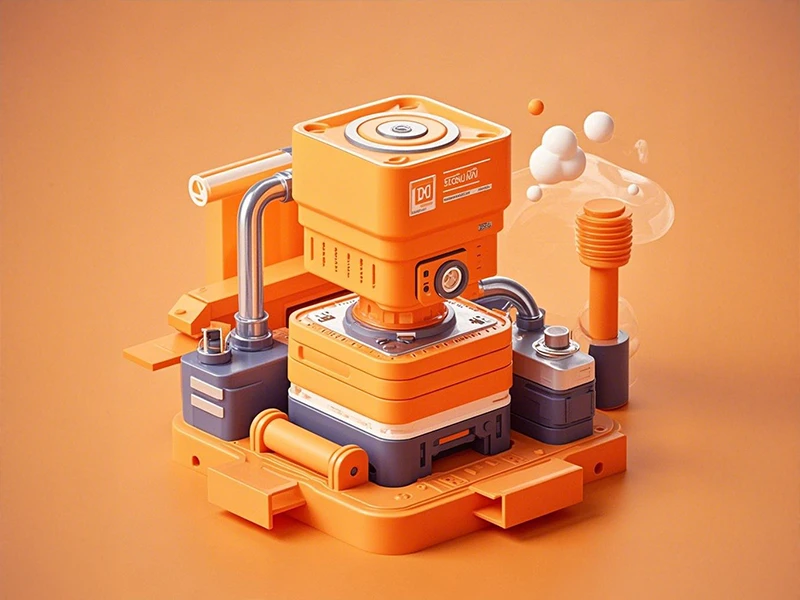
Step 3: T1-V1 Mold Design & Making
Customize, design and making your mold. Make sure you get the satisfies mold.
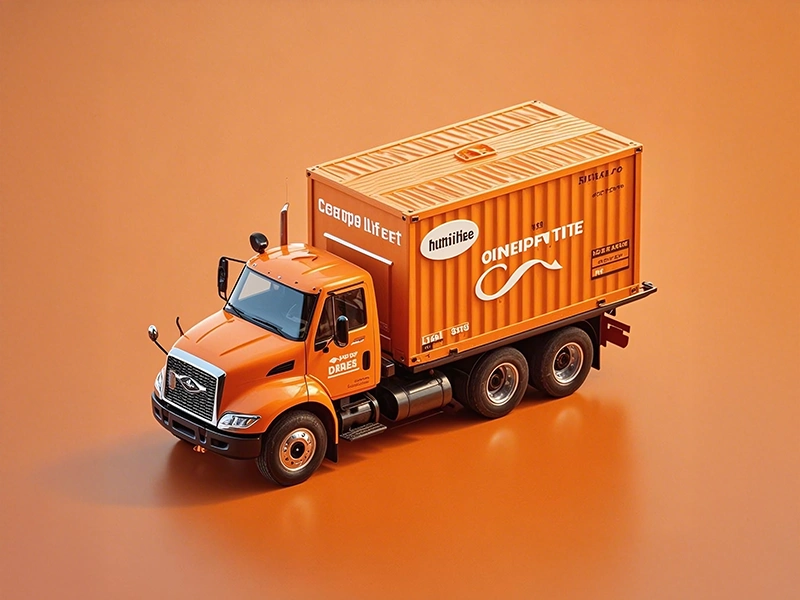
Step 4: Production & Shipping
Manufacturing your products and shipping to your place. Affordable price guaranteed.
Prototyping VS Production Tooling
We can do both types, you can choose according to your need.
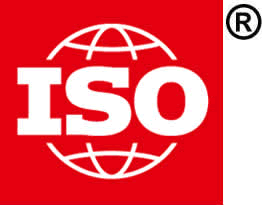
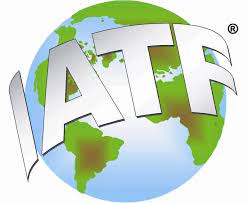
Prototyping Tooling
- Low MOQ from 1
- Cost-effective
- Steel tool
- Low-volume manufacturing
Production Tooling
- Higer quality tooling
- Million molding shot
- Lower parts pricing
Material Options
PP | PE (HDPE、LDPE) | PVC | PS |
ABS | PA (PA6、PA66) | PC | PBT |
PPO | POM | PMMA | TPE |
TPU | PET | PEI | PSU |
PP – GF | PA – GF | PC – GF | PBT – GF |
FR – ABS | FR – PC | FR – PBT | FR – PA |
POE | HIPS | ASA | SAN |
SEBS | EVA | PPA | LCP |
CF – PP | UV – PE | HH – PP | F – PVC |
IM – PC | LW – PBT | TPA | HF – PP |
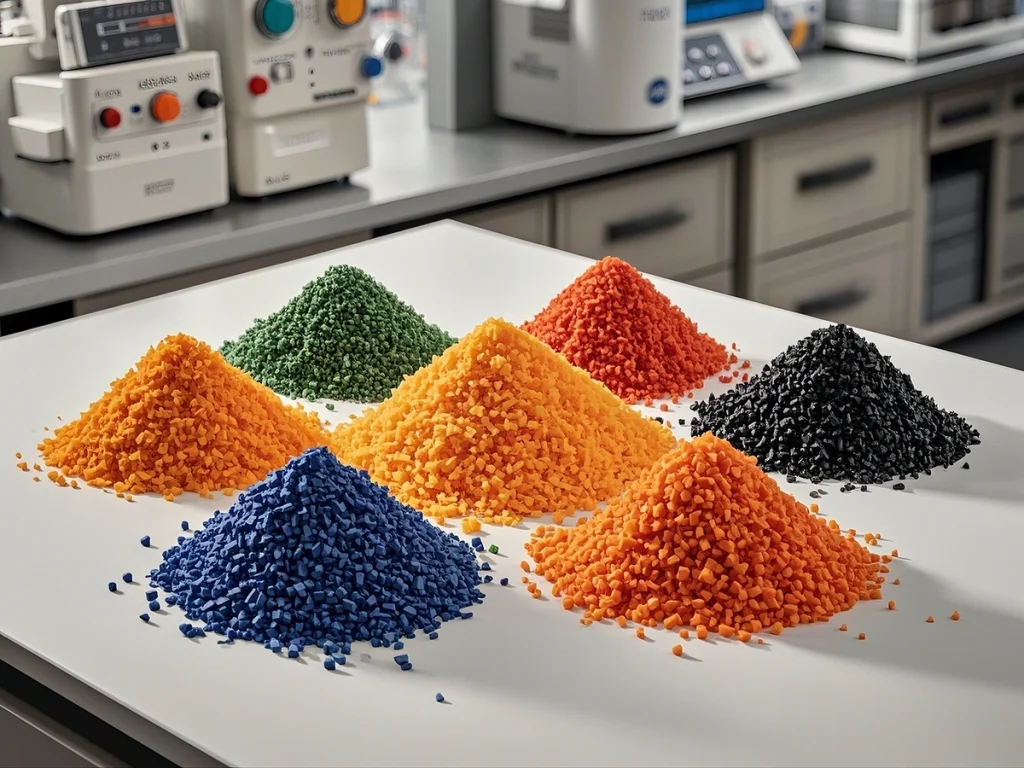
The above materials are the most common stock material options. If your desired material is not listed above, please contact our team here. You may learn more about our other options and custom material applications by clicking here to go to our materials page.
Finishing options
Molded parts can be finished in many ways that may cover purely aesthetic finishes or offer some form of protection to the part. Finishes should beautify and enhance the sophistication and functionality of any part. At First Part, our Injection-molded parts may be finished in any of the following options:
- As manufactured
- Bead blasting
- Pad printing
- Etching
- Textured finish
- Laser finishing
- Semi-Glossy
- Glossy
- Matte
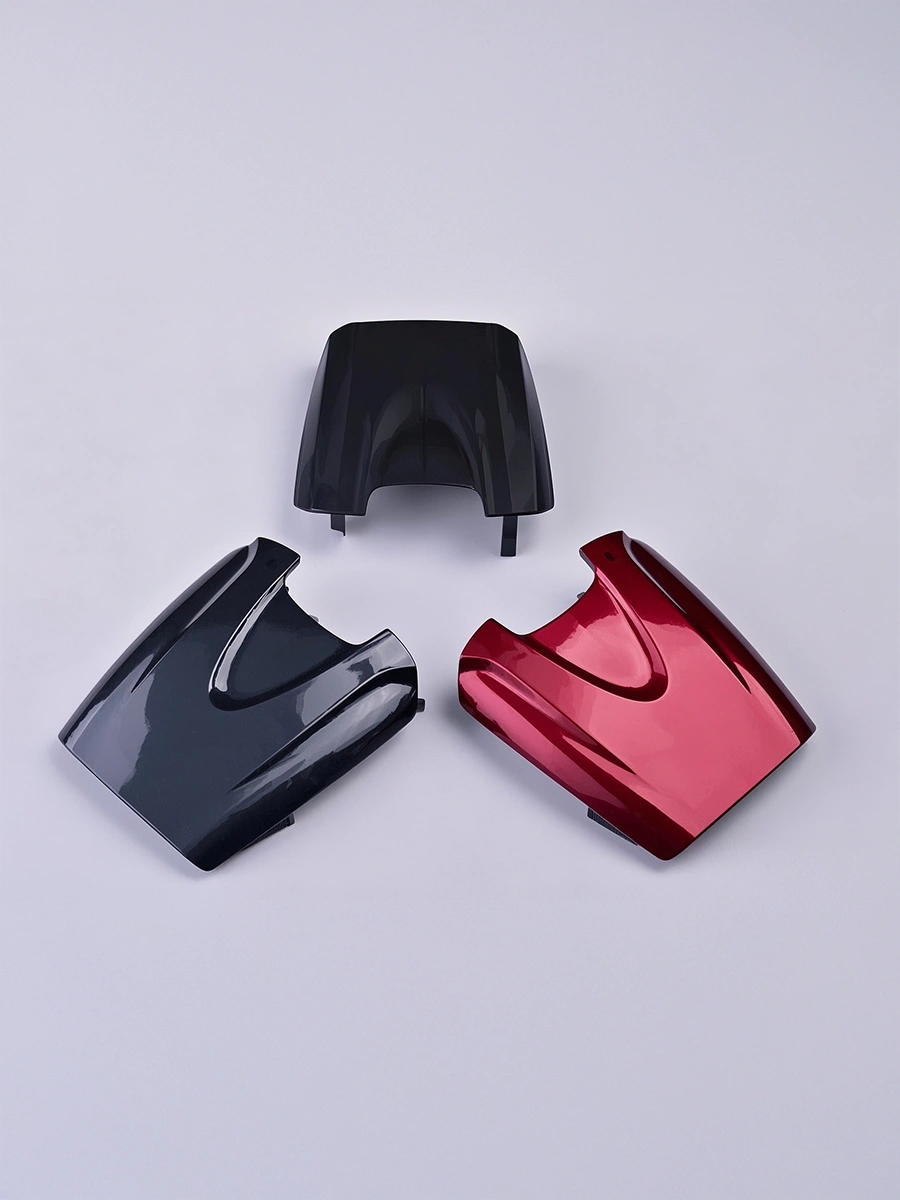
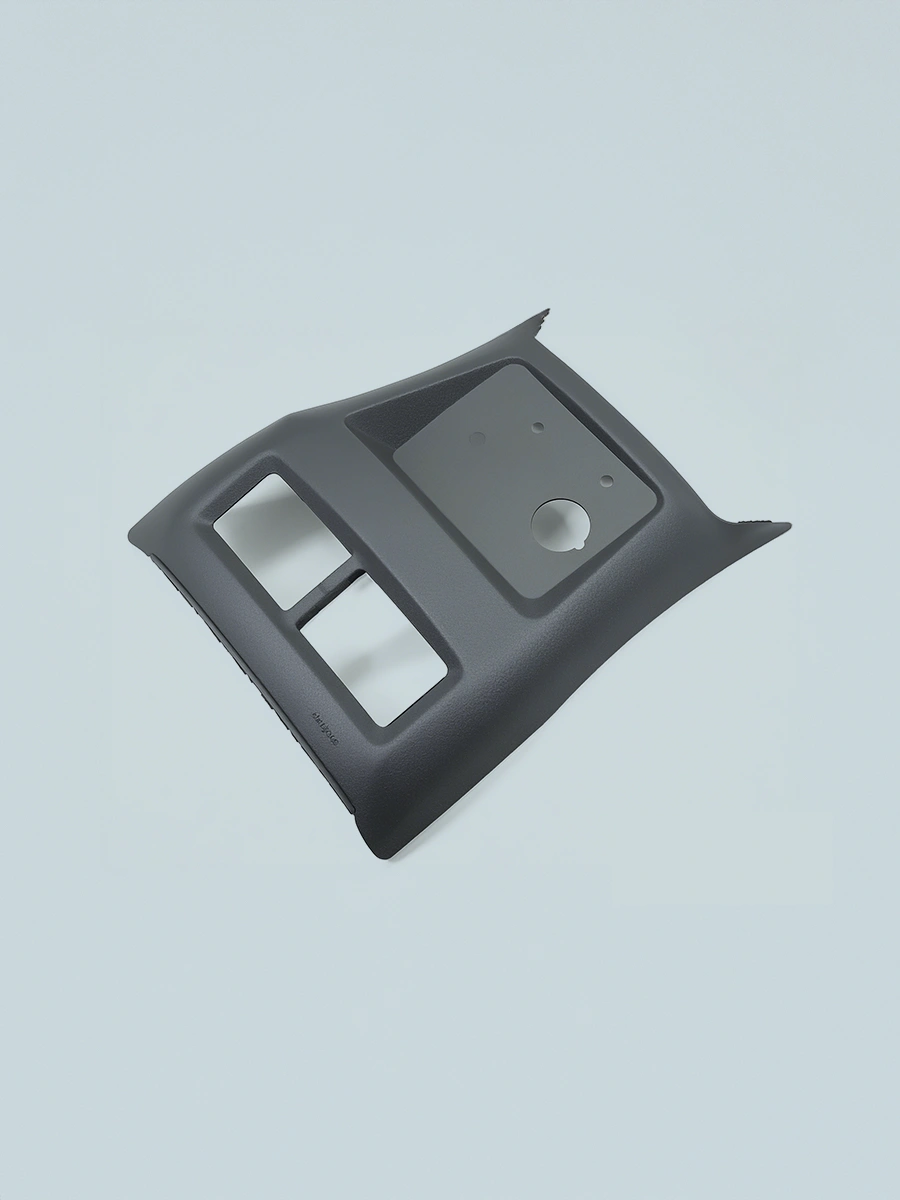
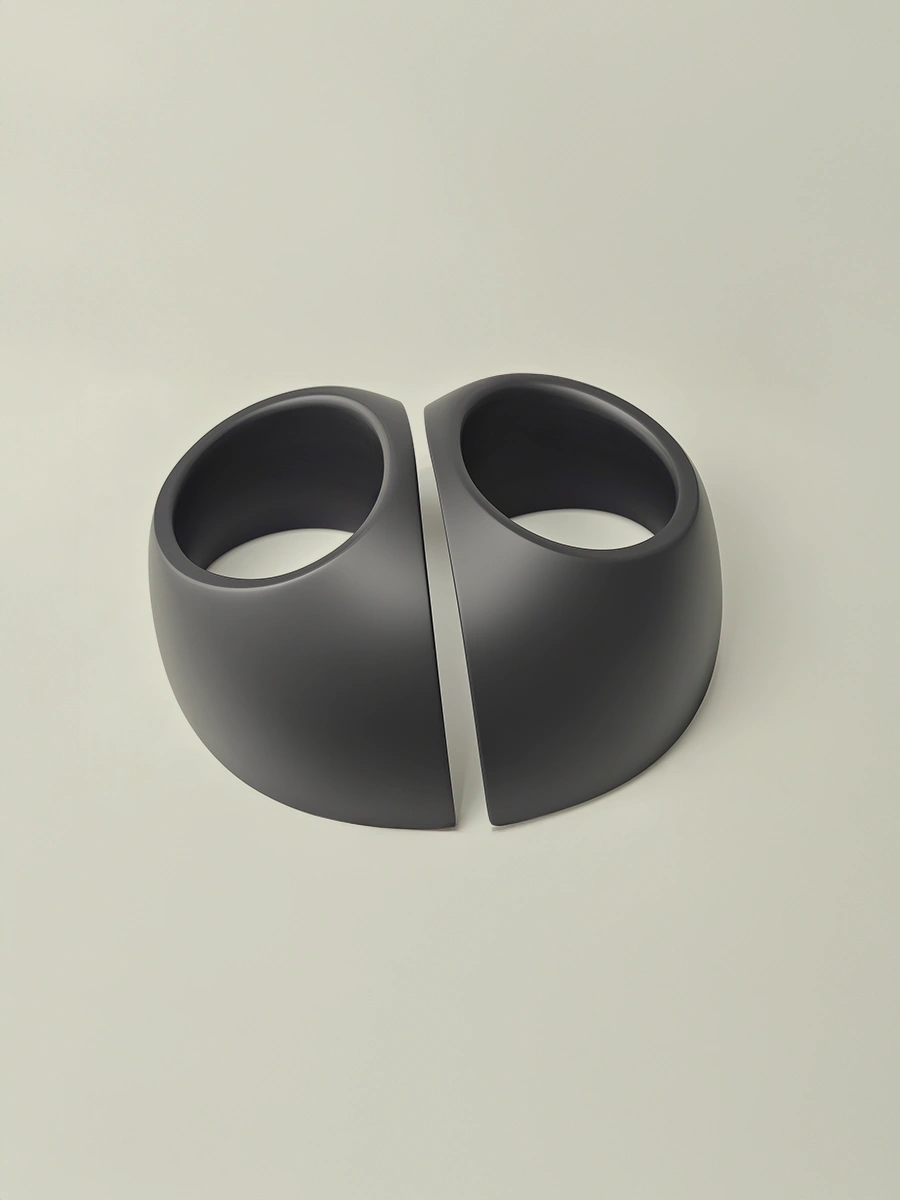
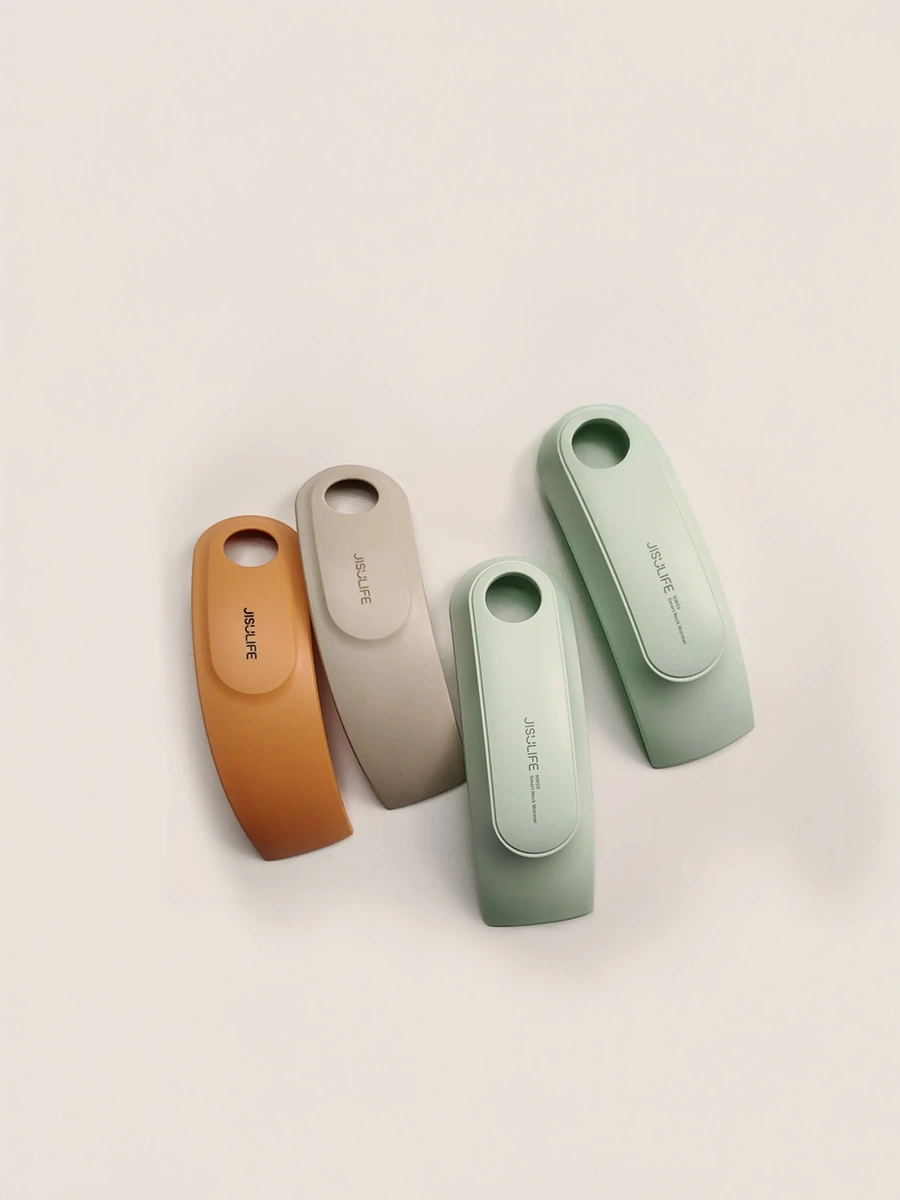
Can’t find the desired finish? Click here to go to our finishing page and learn more about our array of finishing options in detail. We also offer custom finishing touches to help you achieve the desired finish or finishes for various parts.
FAQs – Plastic Injection Molding
What Injection molding capabilities does First Part have?
First Part’s Injection molding capabilities are reliable, precise, and scalable. Our robust manufacturing hubs make us one of the most trusted outlets for general metal and plastic fabrication. Here’s a summary of all our injection molding capabilities.
What are the advantages of Plastic Injection Molding?
Plastic injection molding is one of the cost-efficient methods of making thousands of finished parts quick and accurate. One tooling has been completed, the other parts can be fabricated in large volumes that any other manufacturing technique.
How long does mold tooling take?
Depending on the volume of parts, the need for heat treatment, design, and geometric complexities, a standard plastic injection molding tool can take anywhere between 7 – 10 days to manufacture.
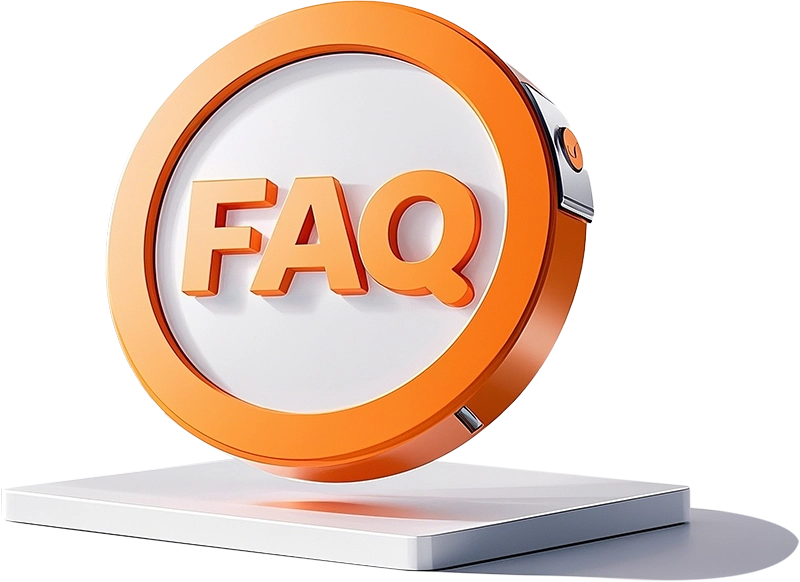