The Most Common Injection Molding Issues when Manufacturing a Plastic Part
Injection Molding is a very technical process that is used in the production of highly durable and quality plastic parts. As is the case with any manufacturing process, without proper care and supervision, an injection molding process may experience a number of issues that will cause suboptimal products to be formed. These defects may also affect the safety and functionality of the plastic part. From small product defects to more expensive molding errors, here are the most common issues that often affect the product quality of an injection molded part:
Flash and Burrs
Flash and burrs arises when molten plastic finds its way out of the mold cavity during the injection molding process. The escaped plastic finds its way out of the mold cavity via the parting line or ejector pins, and then cools without separating from the final product, causing a visible defect that usually appears at the edges of the product.
Products may have flashes or burrs as a result of excessively high pressure during the injection molding process that forces the molten plastic to splash out and escape. It may also occur as a result of prolonged used of worn and torn molds or when a mold is not clamped together firmly.
To prevent flashes, ensure that the clamp pressure is high enough to keep the mold parts shut during the process. Also ensure that you maintain your molds properly and do not use them beyond their prescribed lifespan. Finally, ensure that you mold under optimal conditions with the right operating parameters.
Jetting
Jetting occurs when a molten plastic does not adhere to the mold surface when molding as a result of high injection speeds. Because molten plastic hot melted plastic fluid, it eventually solidifies to pattern the surface of the part to show a jet-like stream.
Jetting arises from running at melt temperatures that are sub-optimal which causes the viscosity of the molten plastic to rise and increase the flow resistance through the mold. It can be prevented by running at the right mold and melt temperature. Jetting may also be prevented by widening the size of the gate to lower the injection speed and ensure that there is enough contact between the mold and molten plastic.
Burn marks
Burn marks are rust-colored defects caused by excessive heating or injection speeds, leading to discolorations on the surface of the injection molded parts. Burn marks can also be caused by overheating of trapped air during molding which then scars the face of the molded plastic.
It may be prevented by reducing melt and mold temperatures. It can also be controlled by lowering injection speeds.
Flow Lines
Flow lines are off-colored lines and patterns that appear on a plastic part as a result of the cooling profile and physical path of the molten plastic during its flow into the mold cavity. It occurs basically, as a result of variations in the speed of flow of the molten plastic as it moves through the contours and bends in the mold tooling cavity.
Flow lines may also erupt as a result of slow injection speeds during molding that caused the plastic to thicken and solidify at varying speeds. To correct and prevent flow lines, up the injection speeds and pressure to optimize the rate at which the cavities are filled. Also, try increasing the temperature of the molten plastic to endure that the molten plastic doesn’t cool easily to leave a trail of solidified plastic marks.
Sink marks
Sink marks are caused by the shrinkages that occurs in the inner parts of an injection molded product. They appear as small craters in the fuller areas of the injection molded part due to an insufficient cooling time for the plastic in the mold. They also appear more in thicker areas because these parts of the product will understandably take longer to cool compared to thinner geometries and structures.
Imbalanced pressure and excessive gate temperature in the mold may also cause sink marks. A remedy for this may be to lower mold temperatures, reduce the wall section thickness, higher the holding pressure and increase the holding time of the plastic in the mold to allow proper cooling and curing.
Warping
Warping is a deformation that arises as a result of the inconsistent and uneven shrinking of different parts of the injection-molded part. This underlying factor is the uneven cooling rates in different sections of the mold that causes the mold to cool different and consequently experience various internal stress in the part. When this internal stress is released, warping occurs. The result of warping is an uneven, distorted and completely unintended shape mismatching the design specifications.
To prevent warping, ensure that you allow enough cooling time for all the heat to dissipate the mold and Dto prevent uneven cooling and allow that the molten plastic moves in a single direction across the mold.
When selecting materials, choose plastic and resins that are less likely to cool as some plastic materials are more prone to warping and shrinking than others.
Short Shot
There are a number of factors that can cause a short shot defect when injection molding a product. This basically occurs when the molten plastic does not fill a mold cavity fully. Short shot can occur due to the molten plastic being too viscous, leading it to solidify before completely occupying all areas of the mold cavities. It may also arise due to inadequate gas venting that prevents the molten plastic from occupying the space occupied by the gas. Because the plastic does not completely fill the mold, the final product inevitably becomes deficient.
A Short shot in the molded part can be prevented by running at higher temperature to heat the molten plastic to have better flow. It may also be prevented by using less viscous plastic that have better flow rates to ensure that all parts of the mold cavity is filled. Finally, design your mold to ensure that there is proper gas ventilation so gas is not trapped in the space the mold is meant to fill.
Weld Lines
Weld lines are lines that appear like planes, and arise from the part where the molten plastic meet each other as they flow into two different parts of the mold. They arise due to partial solidification of the molten plastic, leading to insufficient bonding of the flow fronts in the plastic part.
Weld lines may be prevented by increasing both injection speed and mold temperature. Adjusting your old design to have a single source flow over double or multiple source flow may also help. Lastly, consider selecting a less viscous plastic to ensure that the molten plastic doesn’t solidify as easily.
Surface Delamination
Surface delamination is another common injection molding defect that occurs as a result of extraneous materials that make their way into the molten plastic. In surface delamination, thin layers appear on the surface of the part with some special type of laminate coatings. The contamination does not only affect appearance but also has an effect on the strength of the final product.
Surface delamination can be prevented by upping the mold temperature and ensuring that the plastic to be used for molding is well dried and clean. Also, reduce overdependence on mold release agents which may contaminate the plastic and focus more on a more efficient ejection mechanism when designing your mold.
Need Defect-free Plastic Molded Parts? – Choose First Part
FirstPart offers high quality, issue and defect-free injection molding service for all your plastic part projects in China. We also offer low-volume manufacturing that serve small quantities from 50 to 10000 parts and produce for mass production. Our engineers are always available to advice on the best processes, materials and design optimization to ensure cost-savings, quick turnaround and the production of parts that are 100 percent defect and issue free. Click here to request a free quote now and submit your design for a free evaluation and contact us on how to get started on your next project.
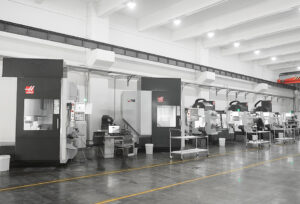