The importance of proper tooling in every machining process cannot be overemphasized. Flat bottom tools present very useful options in rapid prototyping process for a wide array of situations, lending suitability and precision in ways that special-use tools may be unable to deliver.
Tools with flat bottom geometry can be used for straightening, drilling, counterboring and even finishing parts to precision. Here are some of the best applications for flat bottom tools and all the reasons why you should use flat bottom tools more often!
1. Cross-hole drilling
Cross-holes are holing that cross into the path of other holes. When dealing with parts with these shapes and design, tools with flat bottom geometry are less likely to create burrs and push materials out the exit holes.
2. Irregular drilling
Flat bottom tools are very suitable for drilling on surfaces with irregular or spherical surfaces because of their geometry. When drilling with pointed drills, you bear the risk of tool deflection as the machine path may not be defined. The vibrations may also force pointed drills to move across the workpiece, especially if it is an inclined surface.
Flat bottom tools are more stable on workpieces. Their flatness helps to engage the workpiece in a more stable manner, lowering the risk of tool deflection.
3. Angular drilling
Angular or tilted drilling refers to a drilling operation where the drill tool engages the workpiece at an angle. Again, flat bottom tools are more suitable for these operations because they engage workpieces with their flat, outer edges, helping you to lower the risk of tool deflection or unwanted movement during drilling operations.
4. Boring holes
Flat bottom tools are very good for boring and finishing drilled holes. Asides being ideal for crossholes, these tools are also very useful for drilling half holes. The slow helix and low rake on flat bottom counterbore tools delivers more stability, rigidity and control. This makes flat bottom counterbores ideal for delivering the secondary touch that some partially drilled holes require.
Flat bottom tools avails users of more control and helps avoid unintentional part engagement. When working with half holes, there is a general lack of stability that arises from the absence of material. If you elect to use a pointed drill for half hole operations, there is a higher chance of error as the tool doesn’t make contact on the material with its entire cutting geometry.
5. Removing drill points and dishes
Standard drills will often leave drill points and small dishes at the bottom of the created hole due to both geometry and operation. Flat bottom counterbores can help to even out the inconsistencies and dishes at the bottom of the hole. They are also suitable for secondary operations to remove the drill points that are left behind by pointed drills.
6. Straightening holes
It is not unusual to make one or two mistakes when frilling holes in a workpiece. Flat bottom counterbores will help to straighten out misaligned holes when working on unfamiliar terrains, using their flat geometries to even out less than perfect points along the holes.
7. Thin-plate drilling
Thin plates are metal workpieces that are relatively light and thin. Flat bottom tools generate more downward force than most other tools. Because of this factor, tools with flat bottom geometries are more suitable for thin-plate drilling than pointed drills that are more likely to create underside burrs.
Why you should use flat bottom tools more often?
At First, we work with an array of pointed drills, special-purpose and flat bottom geometry tools. Here is our rundown of reasons why you should use flat-bottom tools more often:
• Reduced machining costs
Flat bottom tools can help lower costs by reducing the overall runtime for the job. This is possible because these tools fit exactly as they should, hardly deflect and are very durable and effective in their operation.
• Increased functionality
Flat bottom tools are highly functional and very versatile, performing multiple functions with precision and accuracy. Because of their geometries, these tools are effective for complex operations like thin-plate drilling, angular and irregular drilling without “walking” on the workpiece or damaging the material.
• Enhanced stability
Flat-bottom tools are highly durable and firm on workpieces during operations. Again, because of their geometries, these tools sit perfectly on the material, generating adequate downward falls that make them more stable than other machine tools during CNC operations.
• No burring
Flat bottom tools are perfect for creating straight and neat holes without burrs appearing on either side of your material.
FirstPart CNC Machining in China
FirstPart is one of China’s leading manufacturing hub for Additive, CNC and Conventional manufacturing techniques. We boast of excellent in-house capacity, labor force and logistics while delivering exceptional value for money. Our array of services include CNC machining, 3D printing, Rapid Tooling, Die casting, Rapid prototyping, Plastic Injection Molding, Urethane Casting, Aluminum Extrusion, Post-machining/Finishing services and much more.
As we understand the start-up challenges that is faced by new businesses, engineers and product developers, we offer both mass production, bridge tooling and low-volume prototyping/manufacturing with no minimum order quantities. Our services are flexible, saleable and innovative, with a team of engineers and design experts available to support you through your entire product development cycle.
Click here to get in touch with us and receive a free quote and project review. To contact us via phone or email, or for all other inquiries, please click here.
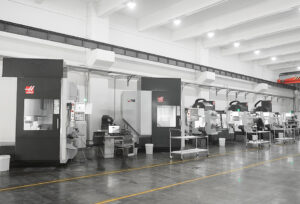