When you need the accuracy and precision of the rapid prototyping services, you can use the Internet search engine to search for effective information about various tools, which can help you make the shape of the prototype more accurate. Some prototype manufacturing companies are manufacturing large prototypes, while some are designed to produce micro prototypes, but not all prototype manufacturers can provide 100% accuracy.
Although sheet metal services can be cut and shaped in many ways, not all methods are as cost-effective and reliable as laser cutting tools, and laser cutting tools can also provide the highest accuracy. Laser cutting tools are equipped with advanced technology, which makes it inevitable to improve and continue its future functions to become very effective.
Laser cutting is a multifunctional tool that can be used to cut and shape various materials, for example. Glass, plastic, wood, sheet metal prototypes, and even stone. The CO2 laser is a widely used cutting tool due to its easy control and high accuracy. In this case, to provide power for cutting, a laser beam made of concentrated CO2 gas is electrically activated.
Fiber lasers often use glass fibers to enhance the potential efficiency of seed lasers. As a result, it becomes a sharp laser that is both powerful and accurate, especially a laser that is more powerful than a CO2 laser. Fiber lasers are commonly used for prototype production of sheet metal because the laser beam is focused and high-intensity.
A crystal laser is not much different from a fiber laser, but it differs from a crystal laser in that it uses both a crystal and a pump diode to generate the beam intensity. Crystal lasers have application and performance potential comparable to fiber lasers. When manufacturing sheet metal prototypes, there are many reasons behind the popularity of using laser cutting as the preferred method, some of which are explained below.
Detailed results may be obtained: because the average size of the laser is a few microns, it is possible to accurately manufacture and cut prototypes of sheet metal services, which cannot be achieved using other methods. As a result, it offers unlimited possibilities. Scalability: Laser cutting tools allow the company to cut any number of prototypes according to customer requirements. These lasers usually do not require adjustments and reassembly to adapt to the design of specific parts. Since the adjustment is inevitable, it is easier to adjust with a laser cutting machine.
Correct edge trimming: For example, using physical techniques sold, cutting a metal plate with a blade can result in improper shape, roughness, flaws and burrs on the edge. For many designs, they will need to be polished or removed, which increases the time required for the end user to receive their product. Using laser cutting charges will eliminate this problem.
As of now, CO2 lasers are still in the leading position of industry standards, and fiber lasers are being rapidly adopted. Although it is a fairly new technology, fiber laser technology is expected to become the standard within the next few decades.
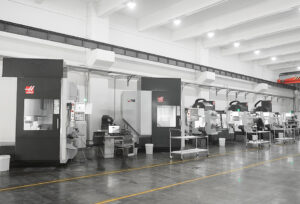