Reducing Part Deformation in Aluminum CNC Machining
Aluminum is inarguably one of the most coveted materials in CNC machining. Its lightweight, high strength, affordability and ease of machinability are all standout attributes, making it perhaps the most used industrial CNC machining material. Even with all of its advantages, part deformation remains a challenge for most Machinists when dealing with aluminum. This is due to its large co-efficient of thermal expansivity and lower hardness that causes it to deform when machining parts with thin walls and thin plates.
One of the ways to reduce this part deformation is to reduce the internal stress of the aluminum during processing. In addition to this, it is advisable to optimize tool usage, run at optimal cutting parameters and using the right machining techniques. Let’s take a look at some of the ways machinists can reduce part deformation when machining aluminum.
• Lower internal stress levels
All materials have some form of internal stress either at rest or during machining. With some synthetic or natural vibration and aging processes, this internal stress of the aluminum blank can be lowered, consequently reducing the chances of deformation during processing. By using aging and preprocessing methods, the excess stress held in the aluminum blanks can be reduced and internal stress reduced in advance before moving onto the main machining process.
• Symmetrical machining process
Symmetrical machining process is a machining technique that processes either part of the workpiece material evenly. The essence of this technique is to avoid the concentration of heat on one part of the material. Symmetrical machining allows for better heat dissipation, which reduces the rate at which thermal deformation occurs. When processing aluminum parts, a symmetrical machining technique should be adopted to optimize parts with large machining allowance to prevent processing only a single face of the material till the final product is obtained, as this pressure can result in deformation.
• Stratified multiple machining
Stratified multiple machining refers to the processing of all layers of a workpiece at the same time. The advantage for aluminum is the reduced force distribution and lower chances of twisting the cavity wall.
This strategy essentially encourages working on the aluminum workpiece layer by layer rather than finishing the whole part in a single go. The advantage of this technique is a more evenly distributed force across the material with less likelihood of deformation.
• Working with the right machining parameters
Getting the appropriate cutting parameter for your aluminium injection moulding machine can go along way in preventing part deformation. From parameters like feed rate, speeds, axial depth of cut, radial depth of cut and cutting force can all make or break your project.
When dealing with aluminum, try to effectively lower the cutting force and heat generated during cutting. You may also try to run at increased machine speed and feed rates to compensative for the lack of processing efficiency that may result from low cutting force. It is advised to run aluminum machining on a high-speed CNC milling machine for efficient results and reduced risk of part deformation.
• Drill first, mill later
Another way to manage aluminum materials when machining is to postpone the milling operation till after some form of pre-drilling is completed. What this does is to reduce the chances of accumulated heat from milling, expansion and part deformation.
Engage in a pre-drilling operation, using a drill tool with a larger radius than that of the milling cutter. Ultimately, you will end up creating a drill hole from which the milling operation will begin. This is particularly important for aluminum parts with cavities.
• Double compression of parts with thin walls
If dealing with aluminum parts intended to have thin walls, you should pay attention to the workpiece clamping style. There are some positions which will make your part deform as soon as the clamping is released. In order to avoid or reduce deformation in thin-walled parts, ensure that the parts that have been pressed are already unclamped to release tension, pressure and restore dimension before engaging in subsequent processes. When finishing the part to its final dimension, ensure that you clamp the workpiece at its strongest point. This will also help machinists to reduce the chances of having a deformed finished part
FirstPart CNC Machining and Aluminum Extrusion services in China
FirstPart is one of China’s leading manufacturing hub for Additive, CNC and Conventional manufacturing techniques. We boast of excellent in-house capacity, labor force and logistics while delivering exceptional value for money. Our array of services include CNC machining, 3D printing, Rapid Tooling, Die casting, Rapid prototyping, Plastic Injection Molding, Urethane Casting, Aluminum Extrusion, Post-machining/Finishing services and much more.
We offer both mass production, bridge tooling and low-volume prototyping/manufacturing with no minimum order quantities. Our services are flexible, saleable and innovative, with a team of engineers and design experts available to support you through your entire product development cycle.
Click here to get in touch with us and receive a free quote and project review. To contact us via phone or email, or for all other inquiries, please click here.
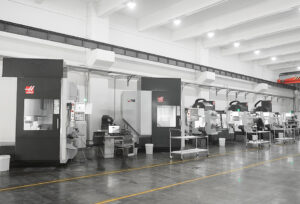