Minimizing Your Cost of Production on All Your Projects
The success of a product, from idea to final product and deployment, depends on a number of factors. Because of how competitive the manufacturing climate is, obstacles like process validation, prototyping challenges, design, patents, funding, investment and manufacturing costs can be the make or break of any innovative product. And while these challenges yet exist, countless products have succeeded in the ever-competitive market. How have these businesses then achieved a winning strategy? For one, successful products can all boast of cost-advantage. What this means is that products are manufactured at the lowest possible cost without any compromise on quality. Once cost has been optimized, manufacturers can then enter an already competitive market at a reduced price to steal market share from established brands.
At First Part, we strive to help all our customers achieve success. One of such ways is to discuss how to minimize the cost of production on your projects, avoid costly mistakes and design for manufacturing and affordability. Let’s get right into it!
Minimize the total individual pieces in your product
Generally, the lesser the individual components in any project, the lower the cost of assembly. When designing on a tight budget, try to make your parts as simple and as minimal as possible. In product design, most of the concerns bother around functionality and less around aesthetics. Try to reduce the number of parts in your design as it will lower the cost of labour, the number of fasters required to put the part together. Lesser parts may also increase the chances of assembly accuracy as it would be understandably easier to put a part of 3 pieces together compared to one with 10 pieces. Once your initial design is complete, assess it for areas where you might be able to combine functions and reduce the total number of final parts. Consider how fewer complex parts can be made using simple mechanics with gears, springs and levers over having many overly simple part with redundant functions.
Increase your production volume
In manufacturing, cost is often inversely proportional to volume of production. This is because when manufacturing, there are some fixed costs and some variable costs.
Fixed costs refers to costs of production that will remain constant irrespective of the number of parts to be produced. Variable costs on the other hand will reduce or increase depending on the number of parts to be manufactured. The total of these fixed and variable costs is the total cost in landing your product.
As manufacturing is very time and capital intensive, one of the best ways to drive down your unit cost (cost per unit) is to produce in higher volumes. This spreads the setup and manufacturing cost over a larger unit of part to help land each part as a cheaper price. Because manufacturing is done with complex machineries, the power cost may remain the same whether you produce 1000 parts or 100,000 parts because of the running capacity of the machine. Production volume can also help you to pick a better material. For instance, some low-volume quantities may require that you use aluminum molds over steel molds because of cost. While aluminum molds are more affordable, steel molds last longer over time, and will generally yield stronger parts. It is therefore advisable to leverage the capacity of the machine to make thousands of part at a single go to reduce your unit cost.
Off the shelf parts over custom parts
Most product and design experts today believe in 100 percent authenticity. Because of this, we notice that many design engineers are always reluctant to use existing off-the-shelf technology in building their parts. This is disadvantageous for two reasons. First, there is more time and effort put into the manufacture of this custom part for your product. Second, you lose out on leveraging the work that has been done by others to perfection. You also risk extending your timeline with trials and errors, capital, testing and process validation of your custom parts during the project.
In order to drive down your manufacturing cost, consider using commercial off-the-shelf alternatives available rather than focusing on building custom parts from scratch. This should help reduce the total cost of production of your part. In advanced productions nearing tens of thousands or millions, consider speaking the manufacturers of some of the parts needed in your product to become a supplier at reduced cost. The potential downside to using off the shelf products however exists that, price fluctuations in the cost of the part may also drive or lower the total cost for your part. The key when manufacturing is thus to find an off-the-shelf part that will help launch your product into the market while you focus of manufacturing your own custom part after you have experienced some form of success in your proposed market.
Try to reduce part weight where possible
Heavier materials often mean that more unit of a material has been put into the production of that part. Explore reducing part weight by using special features such as gussets and ribs to convey functionality such as strength and toughness without wasting material. Also try to limit the amount of material that goes into your part by limiting wall thickness to what is required. Wall uniformity is also important to avoid having some parts of your product stronger than others. Lowering product weight will also reduce shipping and freight costs which is a very important faucet of delivery and logistics for your business.
Design for manufacturing and focus on automation
Using specialized techniques to design your product for manufacturing and affordability. In countries like China, labour is relatively more affordable compared to the USA. Optimizing your design for manufacturing can help you reduce the likelihood of manual interference in the production of your part, and consequently, labour cost. If you stick to good design guidelines, you will also be able to reduce material waste, cut down on the need for assembly and ensure a smooth linear production that will impact turnaround times.
Let First Part(injection mold maker) help you turn your concept into reality
Whether you’re working on a budget or looking to design a complex, aesthetic-driven and functional end part, First Part has the breadth of experience to help you with all your product manufacturing goals. Please click here to contact us, or take a look at our request a quote guidelines to ask for a free quote now and discuss any questions. Let us partner with you and help bring all your products to life. Click here to get started on the path to success.
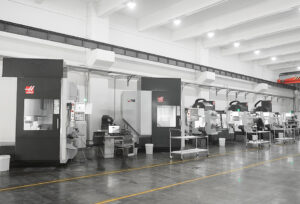