All the differences between Product Prototypes and Finalized Parts
A lot of our readers have been asking about product prototyping and final production. Some of our customers are of the opinion that product prototypes are just as good as finalized designs. Others believe that prototypes are simply low-volume alternatives to mass production. Well, there’s an element of truth to both angles. However, product plastic prototypes and finalized parts are not exactly the same. For one, the materials used in prototypes are often not the same as those for finalized parts. Other differences center around cost, testing, volume and production processes. We have thus decided to take a look at the important differences between prototypes and final products. Let’s get right into it.
Purpose
To begin, we take a look at the core purpose of a plastic prototype versus that of a final product. Prototypes are essentially designed to resemble the final product to a decent level of fidelity. The prototype is the physical iteration of the design that is to be evaluated for functionality, application, potential issues, solutions, optimization and more. The sole purpose of a prototype is to validate a product concept, idea or design, test such design for loopholes and come up with solutions based on the test data that will be used to prevent the finalized part from failing.
The finalized product is one that has already passed all testing. It is the aftermath of the prototype and its purpose is to serve the everyday user or final consumer.
Material
Final products are designed and manufactured with the materials that the product is intended to be sold. Prototypes on the other hand are made from alternative materials that are more affordable and cost-efficient. For instance, parts that are meant for manufacture with titanium may be prototyped with steel, plastic or metal alloys. More often than not, unless material finish is an important part in the product functionality, the prototype will be made from a more affordable alternative material. Engineers may at best, try to minimize the impact of the differences in material on the performance of the prototype. As such, the material substitution between final product and prototype will be detailed and strategic.
Volume
Prototypes are intended to serve as “dry runs” or testing units. Because of this, prototypes will not be manufactured in generally large quantities that finalized products will run. Finalized products will run in either batches or mass production of 1000 to 100000+ units, while prototypes may only be manufactured in 10s, 20s or 50s.
Cost and Quality
Unlike the finalized product, prototypes cannot boast of other important aspects of consumer acceptance and quality metrics. Finalized products will often score very high on performance quality, material finish, user-experience and user interface. Often times, the engineering design and functionality will be the main focus of the prototype.
Also, because of the use of more affordable materials, less finishing and a less complex manufacturing technique, producing a prototype should be cheaper than making a single unit of the final product.
Process
Production process is one significant difference in the manufacturing of prototypes and finalized parts. When producing finalized parts, the volume is usually higher, and as such, mass production techniques are applied. Prototypes in contrast, because of their volume cannot be made with mass production methods. Because of this, the fabrication technique for prototype will be different from the finalized product.
CNC machining, urethane casting and 3D printing are the most popular methods to prototype. These techniques do away with the need for expensive tooling and significant manufacturing overheads that will make running a prototype more expensive. The difference in manufacturing process will most likely reflect on the appearance of the prototype in relation to that of the finalized part that is manufactured with traditional tooling and specialized methods that take extra attention to detail.
FirstPart delivers high-quality rapid prototyping solutions to meet different types of client specifications. Our professional expertise makes us able to turn projects around quickly without compromising on the functionality and quality of your parts. For all rapid prototyping services in china, First Part is your one-stop shop for premium quality services and low-volume manufacturing. Contact us today!
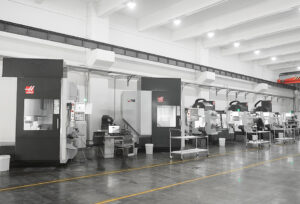