Top Metal 3D Printed Applications
Metal 3D printing has become increasingly popular and continues to challenge the way we think about metal fabrication. One of the reasons for this is the fact that metal parts that are serially printed to mass production are ready to use on demand and equally as good, if not better than metal parts manufactured by conventional techniques.
Polyjet 3D Printing is also special as it offers an array of opportunities to take advantage of the distinct properties of metals and create complex end-use parts. It provides for the direct manufacture of suitable prototypes, jewelries, kitchenware, utensils and consumer electronics at reduced costs and faster lead times.
What are the benefits of Metal 3D Printing?
Before we can delve into the applications of Metal 3D printing, it is essential to understand the benefits of the process. Polyjet 3D printing takes advantage of the design flexibility of 3D printing and the mechanical characteristics of metal. This makes it possible to manufacture lightweight structures, tooling inserts and complex geometrical metallic end-use parts that can serve several industries. The benefits of Metal 3D printing include:
— Geometric freedom
— Automation
— Zero tooling
— Lightweight applications
Three Metal 3D Printed Applications
Low-volume end use parts: 3D metal manufacturing offers a feasible solution to the high costs associated with low-volume manufacturing. Conventional manufacturing processes are chiefly expensive due to the cost of tooling. Metal additive manufacturing helps to rid the cost of tooling, eliminating the need to spread production cost over the volume of parts manufactured.
Metal Prototypes: 3D metal printing is relatively easy to setup and cheaper to execute. Because this process requires very affordable machine setup and no tooling at all, 3D printing offers a way to produce functional metal prototypes that allow designers have accurate metal parts and evaluate design feasibility quicker. No tooling also means that the process is faster and the expensive tooling is avoided. With metal 3D printing, simple changes and corrections can be made to designs and engineers can explore more concepts with faster turnaround. This helps to compress the product development cycle.
Customized tooling: Metal 3D printing allows for the production of special-type tools that are outside generic uses Metal additive manufacturing allows a tailor-made approach that allows for the creation of custom, specialized equipment to meet a particular end use. Because of the absence of tooling costs, these special-type tools can be manufactured without high manufacturing overheads.
Lightweight parts: Metal additive manufacturing allows for the production of super lightweight parts using metals with excellent strength to weight ratio. The advantages of this are numerous. Lightweight metal parts contribute excellent strength to aircrafts and automobiles without impacting the weight of these vehicles. The benefit is lesser fuel consumption and improved engine efficiency.
Functional Mounting brackets: One of the trademarks of the metal 3D printing industry is the ability to produce complex, lightweight brackets in quick times. Metal additive manufacturing offers an alternative for the production of intricate, organic shapes and design that are otherwise impossible to be manufactured traditionally. Metal additive manufacturing bypasses the constraints that thin, complex lattices pose to conventional manufacturing, allowing for the inexpensive production of functional brackets with specialized geometries.
Other ideal applications for metal 3D printing include the manufacture of production tools, ductwork, spare parts, rigid housings, heatsinks and heat exchangers.
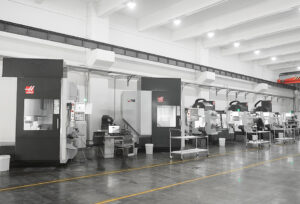