Case study: Interior LED Lamp Processes: Rapid plastic injection molding for volume production Materials: Mold Tool (Reflector Part): 718H / Mold Tool (Lens Part): S136 Reflector Part: — LG CHEM LUPOY RF3208 solid white (Download the material sheet) Lens part: — Bayer Makrolon PC2647 clear (Download the material sheet)
Case study: Interior LED Lamp
Processes: Rapid plastic injection moldingfor volume production
Materials: Mold Tool (Reflector Part): 718H
Mold Tool (Lens Part): S136
Reflector Part: — LG CHEM LUPOY RF3208
solid white (Download the material sheet)
Lens part: — Bayer Makrolon PC2647 clear
(Download the material sheet)
Finish(Reflector Part): High polish
Finish(LensPart):Cavity-Optical polish, core-VDI30
Lead Time:15 working days (10 working days for low volume molding tool)
Mold Life: 100K+Units
Requirement:tooling+molding+ inspection+ assembly+ packing
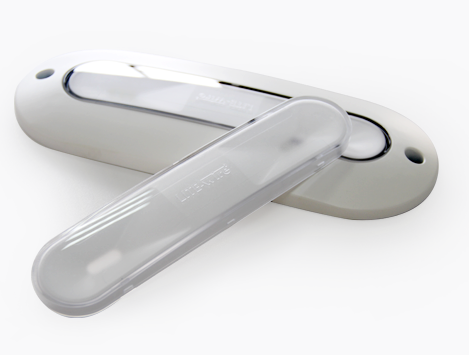
Step One:
Product Presentation
The interior LED lamp is primarily made of plastic and aluminium. The lamp serves the purpose of illumination in car compartments and is produced by the combination of injection moulding and die casting processes.
For the purpose of this project, we aim to introduce two representative components – The Reflector and the Lens.
After being approached by the client who had inquired about the tooling of his products. The client inquired about the tooling of up to 1000 pieces.
After following standard procedures, our sales team replied the client with a quote within 12 hours. For the rapid tooling process of simple structures, First Part China Limited is able to reduce the time of production from the standard 12 hours to 6 hours. This saves our customers waiting time and allows them to spend more time for accessing and evaluating the produced design.
In the absence of complaints and after reaching a unison conclusion with the clients, we evaluated the options and selected the materials “LG brans solid white PC”, “Bayer Makrolon clear PC” due to their excellent transparency properties which is required by LED lamps. We also picked those materials for their high temperature and wear resistance.
At First Part China Limited, we design for purpose and as such, we selected both materials based on the client’s purpose of design and professional input from First Part’s CAD engineers.
The next step in the process is to engage in DFM communication
Step Two:
DFM Design
The DFM design is developed to show the client a feasible design scheme. In most cases, these DFM designs are available in 1 to 2 days. After a detailed review of the 3D models, we create a DFM design for the client. The Tooling design would also be based on the DFM design. Below are some pictures that illustrate the process:
3D model:

DFM: (Reflector Part)

DFM: (Lens)
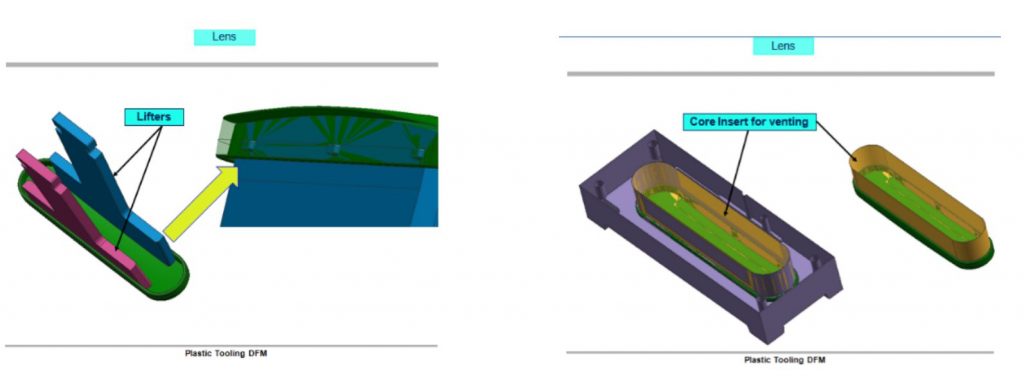
Tooling design:
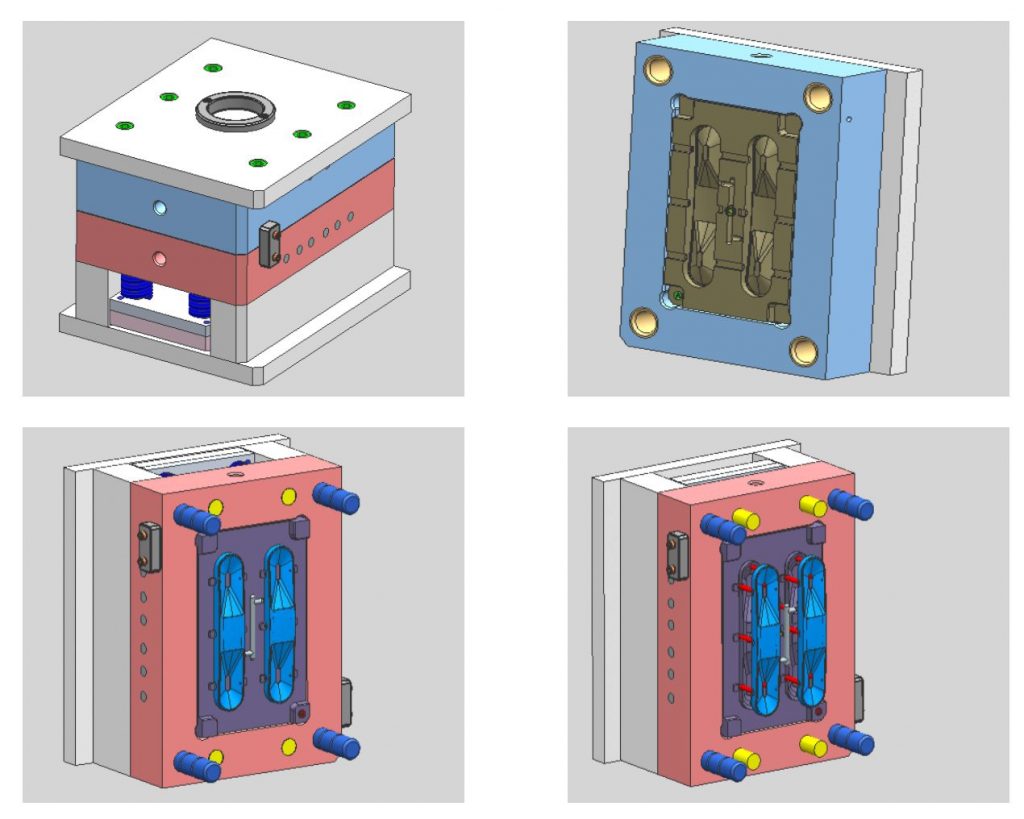
Step Three:
Mold production and Injection testing
Over the next couple of days, the mold production and T1 part injection is done. During the course of these processes, we inject and test some parts while evaluating the results to modify the tooling accordingly. This is important to guarantee that only the highest quality parts are produced.
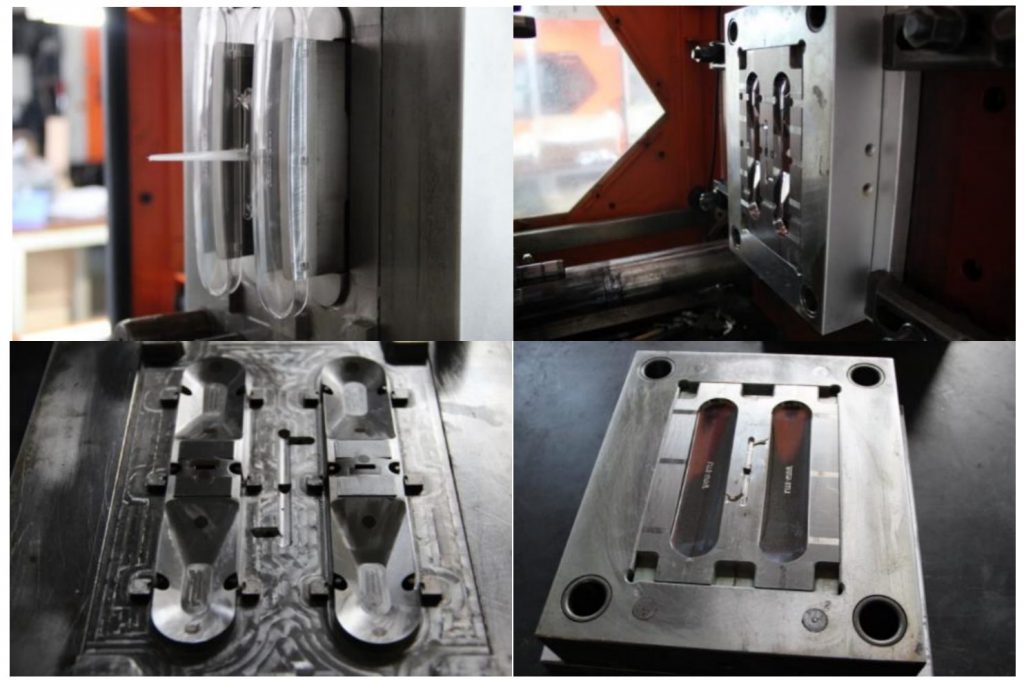
Step Four:
Assembly
The next step is the assembly. This is done in 7 simple steps. We begin by gathering the accessory parts. The process then continues by installing the “O” ring and then the PCB. After these steps, the light-cup is assembled and installed. The next step in the process is to glue the parts and complete the design with a proper finishing. In simple flow chart, we have
1. ACCESSORY PARTS
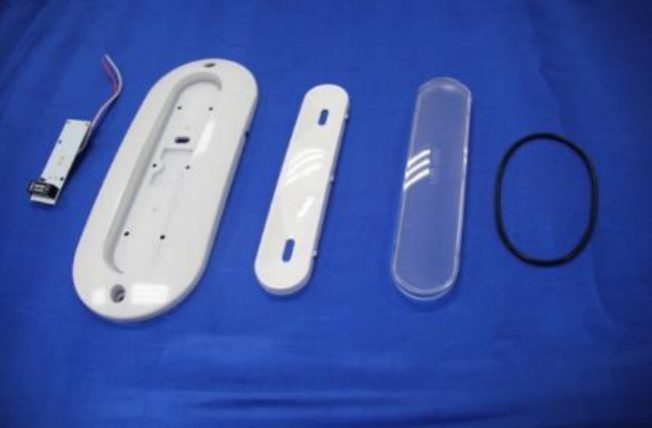
2.INSTALL THE O RING

3. INSTALL THE PCB
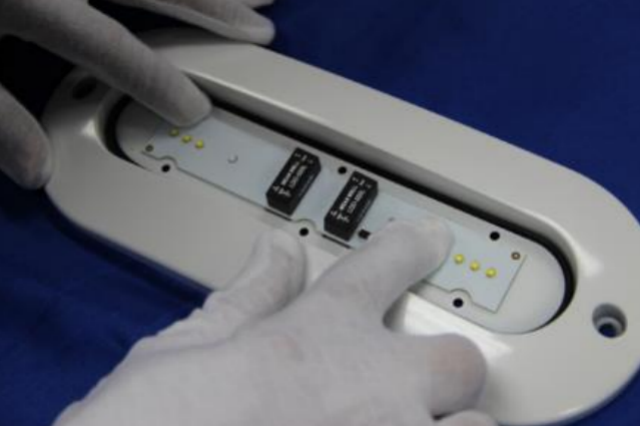
4. Assemble the light-cup
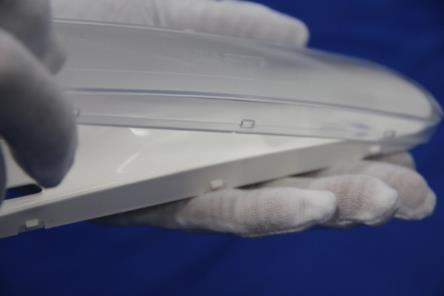
5.Light-cup install

6.Gluding

7. Finished product

Step Five:
At First Part China Limited, we pride ourselves in making only the best quality products for clients. Our QC department is then saddled with the responsibility of checking for perfection.
All parts are inspected for conformity and quality. The details are accessed from the 3D model to ensure that all the dimensions and sizes meet specifications. We also include a series of lighting, sealing test, dimension checks and so on.
Sealing test
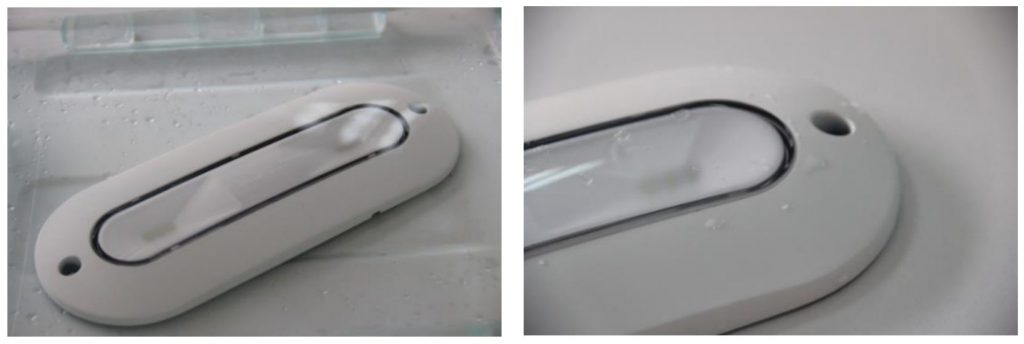
Inspect the dimensions
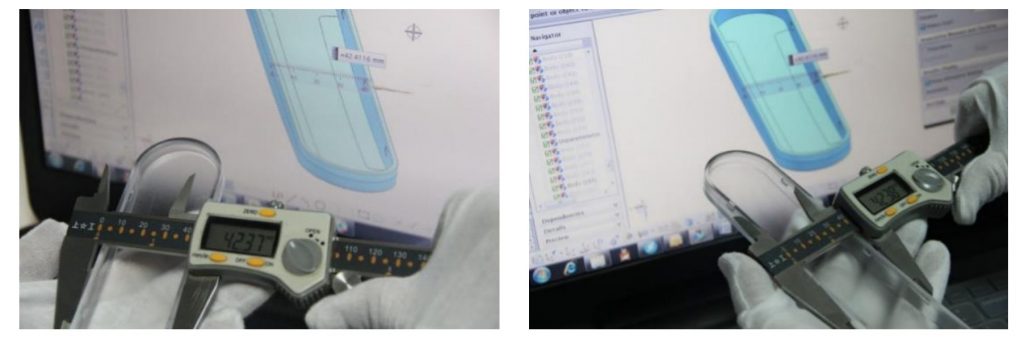
Lighting test
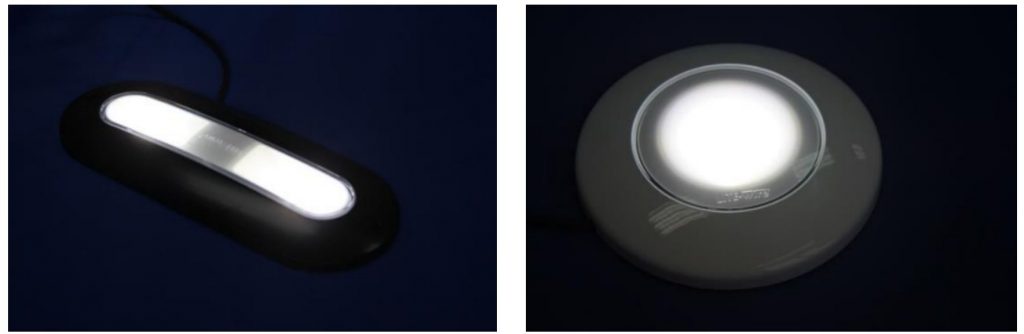