Precision injection molding is one of the most reliable production techniques in the industry today. Along with CNC machining and 3D printing, injection molding is one of the biggest income streams for most manufacturing hubs. Great as it may be, engaging a molding project is not cheap. Because of how the process is executed and the pre-molding requirements, injection molding is often used for the production of final designs and end-use parts that have already passed testing and feasibility studies. In fact, cost is one of the major reasons why injection molding is not often employed in prototyping
The biggest drivers of cost in any injection molding project are the operation run time, material cost and most importantly, tooling costs. The tooling cost is most expensive as it produces the master from which the other parts are molded. While the operational and material costs are proportionate to the volume of parts to be produced, the cost of tooling is fixed irrespective of the parts to be made. Therefore, injection molding is never recommended for making low-volume runs as tooling cost may account for over 50 percent of total cost.
So, how then does injection molding become more affordable? First, by using some design techniques, one can drive down part complexity, avoid part assembly and operation run time. In the first part of this article, we have considered how overmolding, DFM, family molds, material cost and cosmetic reduction can all lower cost. We have now gathered a few more tips to help you reduce cost in your next injection molding operation with us at Firstpart in China.
Design to avoid undercuts
Undercuts are features in injection-molded parts that prevent damage of the molded parts when ejecting them from the mold. Undercuts may include holes, protrusions, recessed areas, cavities and more. They make the design complex and more expensive to obtain. The solution to keeping mold prices low is to work with your design expert to explore alternatives to undercuts. In some cases, undercuts may even complicate your part ejection. Eliminating undercuts in side-action, sliding shut-offs or pick-out mold techniques is often a challenge, this is why we recommend using straight-pull molds at every opportunity.
Reduce part size when possible
When possible, try to scale down the overall size of your part to achieve faster production and quicker solidification. Making smaller parts also mean that your material can produce extra volumes and a reduced cost of tooling/mold production. If size is not critical to your design, some 10-15% shrinkage can play a big part in reducing your cost.
Reduce wall thickness where possible
While having a decent inches of wall thickness is important to prevent structural fail and ensure dimensional stability, reducing the wall thickness of your end part will proportionately reduce the material consumed and operation time. By lowering your wall thickness by 1mm for instance can reduce the production time of each unit of plastic part by up to 60 percent.
Thinner walls also facilitate faster cooling, quicker mold filling and solidification. It is important to re-emphasize that wall thickness should be lowered moderately. Walls too thin will lead to reduced physical and mechanical performance. When reducing wall thickness, use features such as ribs and gussets to deliver complimenting structural support.
Consider post-processing operations
If you have to use injection molding for low-volume manufacturing (no more than 1000 parts), you can save some cost by reducing the detail in your mold. Consider post-processing or secondary operations that can help you convey the required feature over incorporating that feature into your design and mold. For instance, you can avoid using side-action cores by making your tooling and drilling a hole in the part post-production. Asides the cost of placing the hole sides into the mold tool, the time it will take the machine to produce each part will be longer. This translates into an extended operation and runtime.
Avoid side-action cores
Side-action core refers to a type of mold mechanism when manufacturing end-use parts. It enables easier withdrawal of molds with undercuts. It is also useful when dealing with parts where detailing is important, and cost is not a bother. To reduce tooling cost by up to 30 percent (saving up to $1000), stick to the conventional straight-pull molds when possible and avoid design complexities.
First Part Injection Molding Services in China
FirstPart offers excellent quality, plastic injection molding services for a wide array of plastic part projects in China. We also offer low-volume manufacturing that serve small quantities from 50 to 10000 parts for small and medium scale establishments. Away from low-volume manufacturing, all our factories boast of an always-running mass production capacity for CNC, 3D printing and Injection molding services. Our engineers are always available to advice on the best processes, materials and design optimization to ensure cost-savings, quick turnaround and the production of parts that are 100 percent defect and issue free. please do not hesitate to request a free quote now and submit your design for a free evaluation and contact us on how to get started on your next projects.
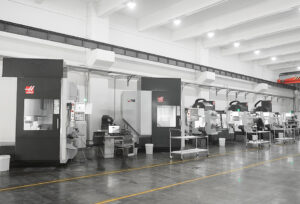