Aluminum Extrusion Service
- Utilizes international-standard mold designs, ensuring dimensional tolerance ≤0.1mm.
- 72-hour prototype turnaround with 30% shorter mass production cycles.
- ISO 14001 compliant chromium-free surface treatment.
What is Aluminum Extrusion?
Aluminum extrusion is a production process used to produce aluminum parts by forcing semi-molten aluminum through a shaped opening in a die using hydraulic pressure. The result is an elongated aluminum part with a profile similar to that of the mold.
The mold in aluminum extrusion is made from hardened steel tools. The shape complexity can range from simple boxes to more complex geometries like electrical heat sinks and vehicle frames.
At First Part, we use several aluminum profiles and materials for extrusion. The most common alloys are the 6061 and 6063 profiles. Our aluminum extrusion profiles have been optimized to enhance the properties of the raw aluminum material. Through controlled processing, First Part can make finished parts that are more durable, rigid, and easily adaptable.
Rapid Prototyping & Low-Volume Aluminum Extrusion Services
First Part specializes in top of the line aluminum extrusion services, working with multiple aluminum profiles to deliver high-quality parts with intricate designs to suit all your product needs. We take advantage of our design flexibility, production capacity, and rapid prototyping methods to use our aluminum extrusion to make end parts for construction, automotive, electronics, and transportation uses quickly and affordably.
Our one-stop service offerings mean that you can combine CNC machining and aluminum extrusion to fabricate parts with complex geometries, excellent strength-to-weight ratio, and impeccable corrosion-resistance. A host of post-extrusion operations can also be carried out with our CNC machining services.
Working with First Part allows you to leverage our dependable quality control systems and process optimization techniques that put us ahead of the competition, ensuring that high-grade aluminum extruded parts are delivered to your doorstep in as fast as 2 to 3 weeks.
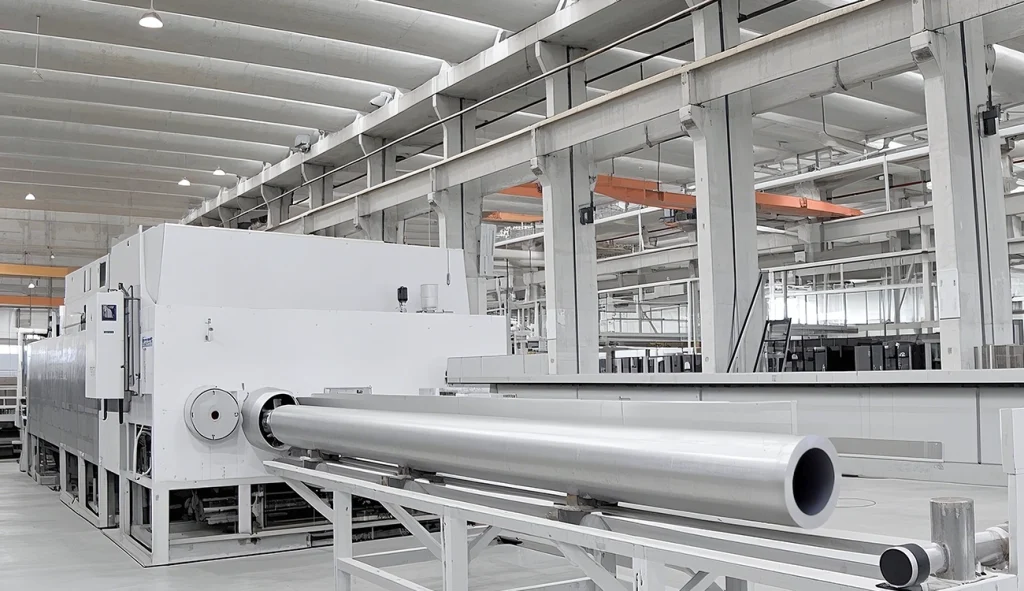
Our experience has allowed us to leverage our machine capabilities to deliver low-volume batch production of as little as 50 to 1000 units, while operations are very scalable to achieve up to 10,000 parts at an even lower cost-per-part. Post-production, all parts can be further processed with anodizing, drilling, tapping, or machining to protect, engrave, or improve your part’s ergonomics.
Our Aluminum Extrusion Process – A Promise of quality!
At First Part, we understand all the factors that go into producing high-quality aluminum parts. This is why we ensure stringent quality control systems to choose the best profiles for your end-use and use other fabrication and post-production methods to improve your part’s characteristics and functionality. After receiving your order, we shall proceed to:
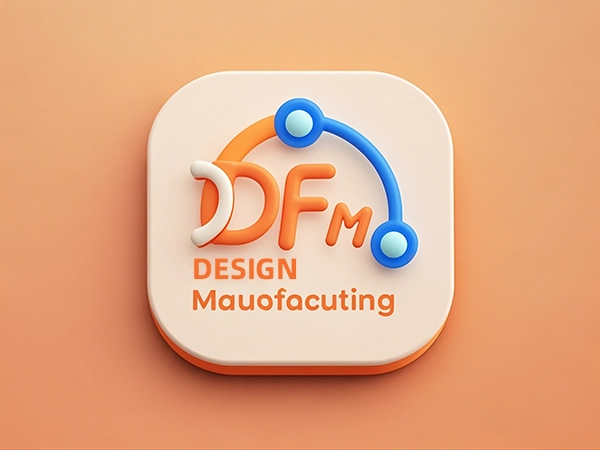
Conduct complimentary Design for Manufacturing (DFM) analysis to optimize part feasibility.
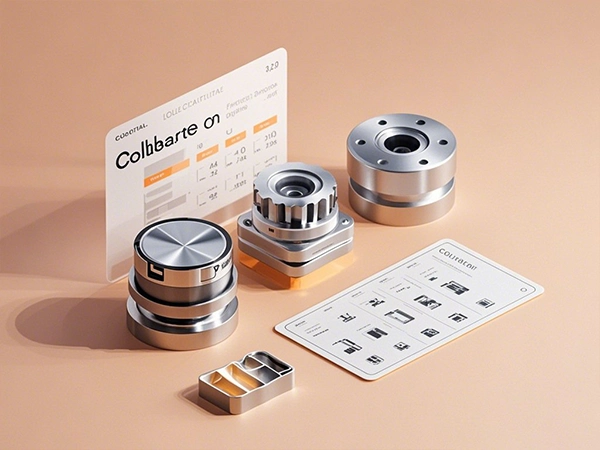
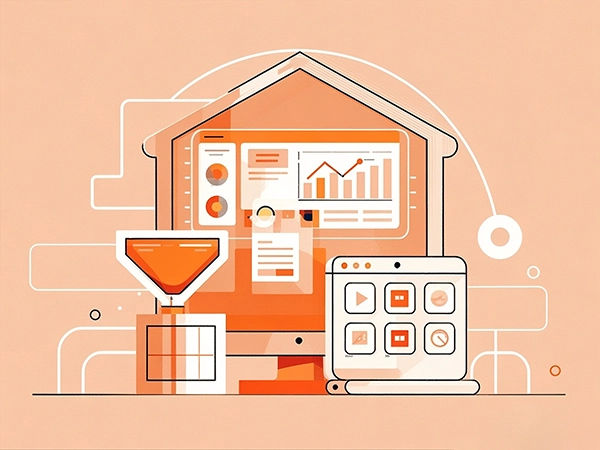
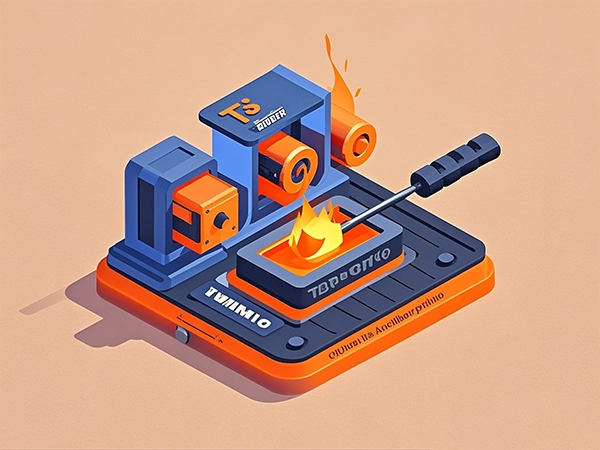
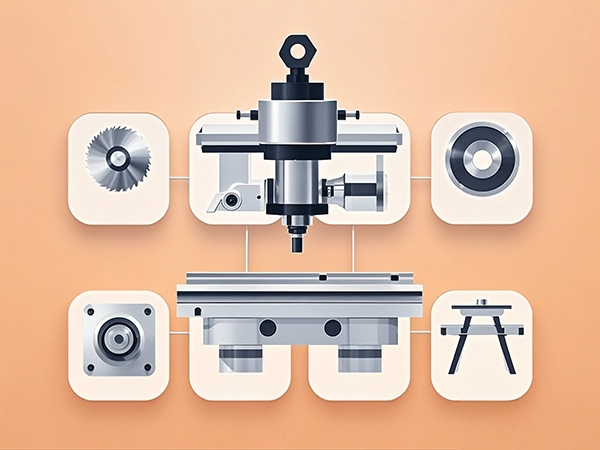
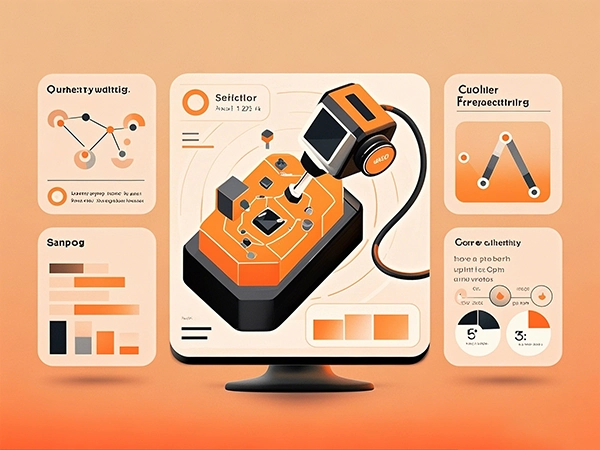
Aluminum Extrusion Applications
High-strength application
Aluminum extrusions can be finished with several customized touches to optimize your part functionality and product needs, allowing you to complete your piece in bespoke specifications.
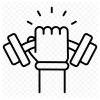
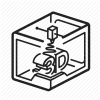
·Rapid prototyping
The low tooling time and tooling cost makes aluminum extrusion a favored method of rapid prototyping, part testing, and design evaluation for quicker product launch and market entries.
Custom-use parts
Aluminum extrusions can be easily tailored to make a variety of parts as required. Product developers and designers can elect to do without the standard extrusion profiles and make specific functional parts that meet your project’s aesthetic, strength, mechanical, and geometric needs.
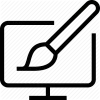
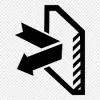
Reflective applications
When finished with particular surface touches, aluminum extrusions can be used for lighting applications and high-reflectance uses. It can also be used to shield components from light, radio waves, or infrared waves.
High conductivity end-uses
Aluminum extrusions have excellent thermal and electrical conductivity. Based on the weight and cost involved, aluminum parts generally better conduct heat and electricity than other common metals. This makes extruded parts very suitable for heat exchangers, dissipators, electrical connectors, and other components. When compared dollar for dollar, aluminum is twice as conductive as copper.
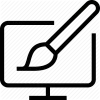
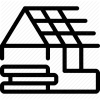
Framing
Aluminum extrusions can be used to make long lengths of part frames, chassis, and enclosures. Because of their easy machining, they can be fabricated to make assembly components and part frames held together with inserts. A typical example is the framing for solar panels, power units, housings, picture frames, and window frames.
Aluminum Extrusion Material Options
Aluminium
- 6061
- 6063
- 1060
- 3003
- 3004
- 2024
- 5182
- 4043
- 6042
- 6262
- 6463
- 6005
- 7050
- 7075
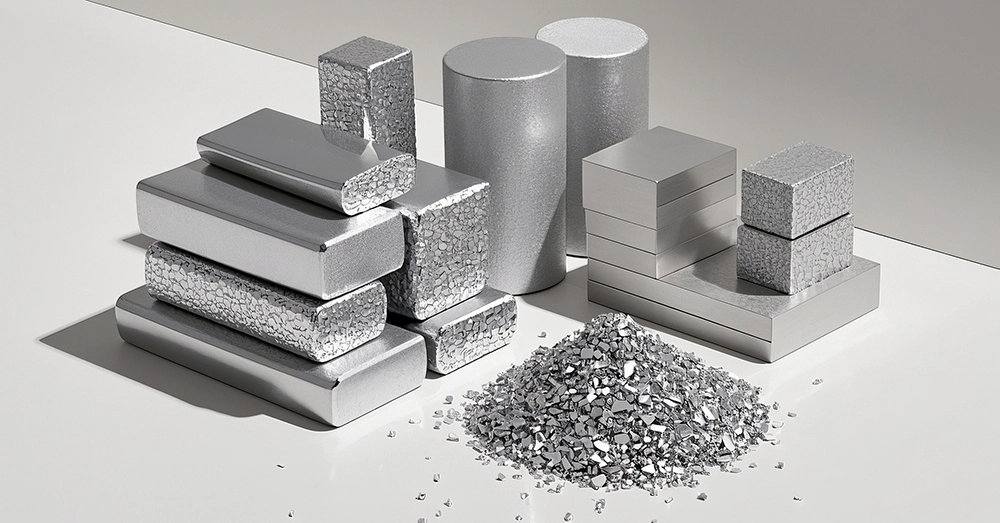