Die Casting Service
- High-pressure die casting for zero-defect manufacturing
- Multi-material solutions with real-time quality analytics
- Smart supply chain integration from prototyping to mass production
What is Die Casting?
Metal die casting is a production process used to make geometrically-complex parts with attractive finishes through custom-made steel mold. The process is quite similar to injection molding, where molten metal is forced into the die to create casted parts. The cast parts take the shape of the die and solidify as the die/mold cavity cools. On cooling, the final piece is removed and post-processed to bring it to the desired finish. Die casting is the most effective approach to making medium to high units of metal parts for end-use.
Die casting allow for the creation of high-quality metal parts with high accuracy and ensures that the process is highly repeatable. The die casting process is carried out with the use of a furnace, the metal material, the die casting equipment and the die itself. Aluminum, zinc and magnesium are the most common die casting alloys.
Die Casting Services At First Part
First Part offers professional one-stop die casting services for making large units of high-quality metal parts with excellent strength, geometry, and finish through the use of reusable molds. Our die casting services are very robust, encompassing a range of operations from mold making, part casting, machining, polishing, and other finishing options.
Our service is a guarantee of quality from start to finish; our quality control and assurance units ensure your raw materials’ quality while casting parameters are fine-tuned for optimal quality in your finished parts. With First Part, you can rely on the quality of excellence from our professional service and cost-effective rates for making your casted parts with speed and precision.
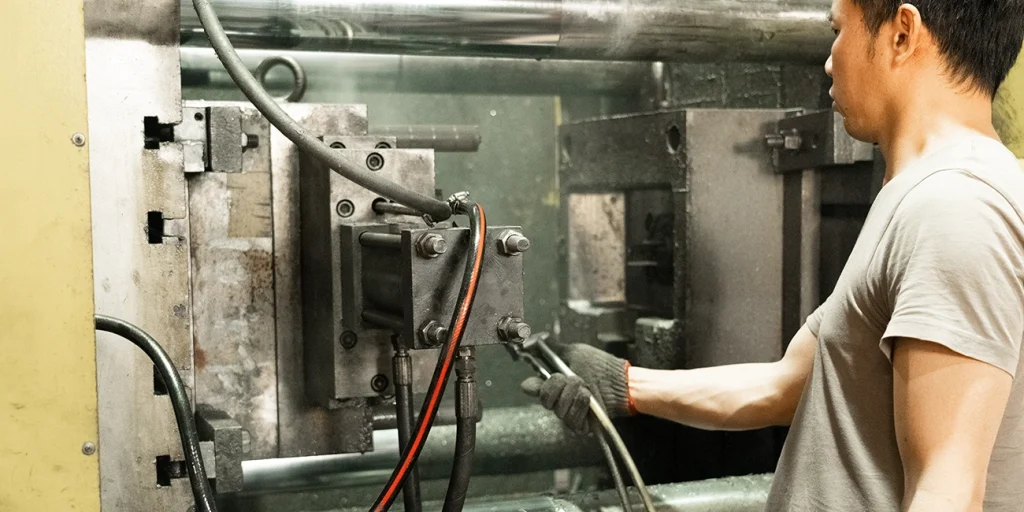
Die Casting or CNC Machining?
Both die-casting and CNC machining can be used for the manufacturing and processing of metal parts. So, how can you know which manufacturing process should be adopted for your products?
Die Casting Dominates in
- Hyper-scale structural systems: EV motor endplates with vacuum-assisted Mg-Al casting (5,000+ units)
- Nano-surface replication: VR headset frames mimicking carbon fiber weave via conformal cooling channels
- All-in-one functional integration: 5G base station housings with EMI grids cast-in
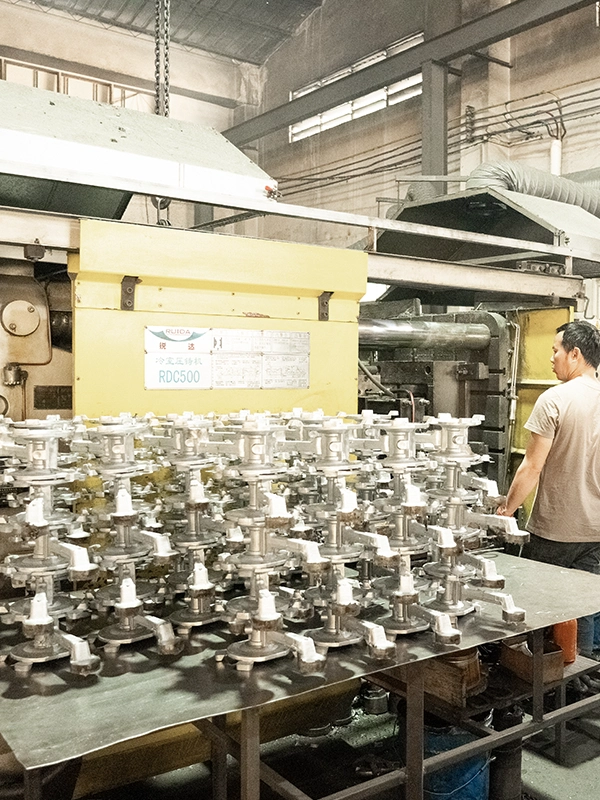
CNC Machining Excels at
Metastable material challenges: Inconel 718 rocket nozzle liners with cryogenic stability
Topology-optimized geometries: Lattice-structured satellite payload adapters requiring 5-axis undercuts
Hybrid micro-features: Implantable neurostimulators combining 316L steel and PEEK surfaces
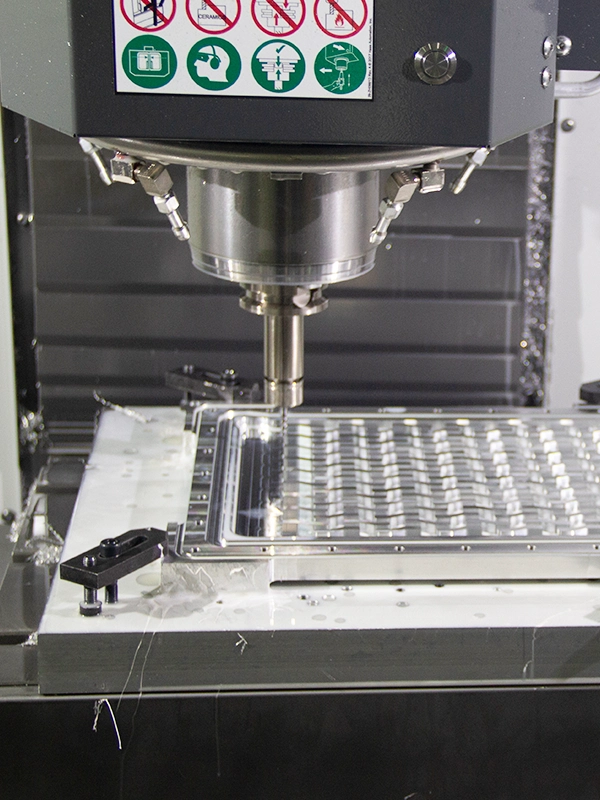
Die Casted Parts Gallery
Unlimited Elements Error: Error in widget Masonry & Justified Gallery, You have some other plugin that loaded another version of twig. It's uncompatable with unlimited elements unfortunatelly.