Quality Control and Inspection
- Real-Time Defect Detection: 3D Scanning (±0.005mm) & XRF Spectroscopy
- Full Traceability: ASTM/EN Compliance with Digital Batch Reports
- Stress & Durability Testing: Thermal Cycling, Salt Spray (1000+ hrs)
Developing products and prototypes with high quality design and parts requires a specialized, stringent and refined quality control process. At FirstPart, we have developed a highly effective inspection and quality control technique that helps to appraise all incoming raw materials and finished products.
Our quality control process combines expertise and experience with advanced equipment for measuring and reviewing client specifications against produced samples before final runs.
Our In-house inspection equipment
- Altimeter
- Olympus Innov-X Delta DS-2000 XRF handheld analyzer and workstation
- Coordinate measuring machines
- Surface roughness tester
- Video measuring machine
- (HRC) Hardness Tester
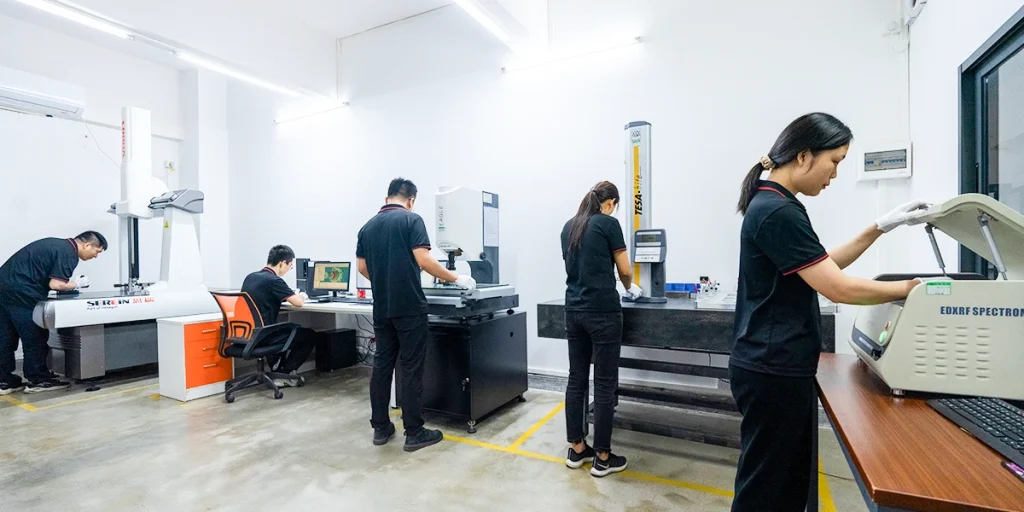
FirstPart inspection and quality review follows a systematic process:
Warning: parse_url() expects parameter 1 to be string, array given in /www/wwwroot/firstpart.com/wp-content/plugins/unlimited-elements-for-elementor-premium/inc_php/unitecreator_params_processor.class.php on line 1596
Warning: parse_url() expects parameter 1 to be string, array given in /www/wwwroot/firstpart.com/wp-content/plugins/unlimited-elements-for-elementor-premium/inc_php/unitecreator_params_processor.class.php on line 1596
Warning: parse_url() expects parameter 1 to be string, array given in /www/wwwroot/firstpart.com/wp-content/plugins/unlimited-elements-for-elementor-premium/inc_php/unitecreator_params_processor.class.php on line 1596
Warning: parse_url() expects parameter 1 to be string, array given in /www/wwwroot/firstpart.com/wp-content/plugins/unlimited-elements-for-elementor-premium/inc_php/unitecreator_params_processor.class.php on line 1596
Warning: parse_url() expects parameter 1 to be string, array given in /www/wwwroot/firstpart.com/wp-content/plugins/unlimited-elements-for-elementor-premium/inc_php/unitecreator_params_processor.class.php on line 1596
Unlimited Elements Error: Error in widget Horizontal Timeline, You have some other plugin that loaded another version of twig. It's uncompatable with unlimited elements unfortunatelly.
Our In-house inspection standard
Physical Quality Control
Precision-Engineered Quality Control: Ensuring Tight Tolerances in Critical Dimensions & Geometry.
Material Quality Control
Assurance checks to ensure that supplied materials are of the right grade, strength, elasticity
Visual Quality Control
Advanced testing ensures color, reflection, and absorption meet specs, with finishes guaranteed for cosmetic consistency in precision parts.