Overmolding & Insert Molding Services | First Part
On-demand Manufacturing, Pilot Testing, and Bridge Tooling
Firs Part’s Insert Molding and Overmolding is a great way to make on-demand prototypes and cost-efficient tooling by combining metal and plastic into a single part. Our insert and overmolding processes are designed to help you create high-quality, functional parts using a range of thermoplastic resins and liquid silicone rubber from affordable molds.
What is Overmolding & Insert Molding?
Overmolding and Insert molding are injection molding techniques used for making composite parts. At First Part, our robust injection molding services make composite parts using both over-molding and insert molding. Additionally, we can combine both injection molding and over-molding processes to create highly functional end-use parts.
Overmolding
Over-molding is used to make a single part in many materials. The idea is to leverage various material properties to deliver a more functional part with improved aesthetics, grip, environmental resistance, and handling properties. The process adds another layer of injection-molded material (usually thermoplastic or liquid silicone rubber) over an earlier injection-molded part. (substrate)
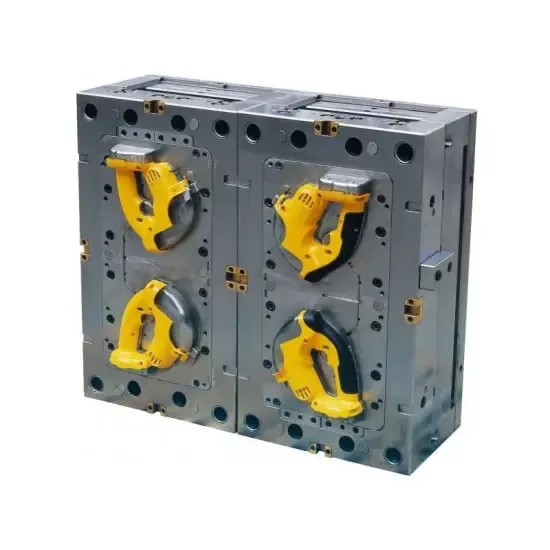
Overmolding can be executed with a multi-barrel injection mold device, adding a subsequent plastic material just after the substrate material is formed. Overmolding creates a rigid bond between the materials and eliminates the need for separate part molding and assembly in creating improved injection-molded parts.
Overmolding is a cost-effective way of making composite parts that will usually require assembly. With over-molding, the first part is molded as usual, while the over-molding process follows to add a new layer of injection-molded plastic to make more durable, scratch-resistant, or more ergonomic parts. Examples of ove-rmolded parts include Toothbrushes with rubberized grips, Print circuit boards, RFID, Steering wheels, Power tools, Phones, and Hand tools.
Benefits of Overmolding
The benefits of overmolding include:
· Enhanced grip and ergonomics
· Abrasion-resistance
· Electrical insulation
· Waterproof sealing
· Better sound absorption and reduced vibration
· Cost-savings
· Eliminates part assembly
· Faster production cycles
· Creates part with tight tolerances
· Texture and design versatility
Insert molding
Insert molding is a part molding technique that involves the injection of plastic material into a mold cavity before a plastic injection molding cycle. It is used to make single-piece parts where a plastic resin encapsulates a prefabricated part (usually non-plastic).
The insert molding process is executed by placing the inserts into the molds, closing the mold, and melting the plastic pellets into the injector barrel. The melted resins are shot into the mold to flow around the captured inserts. Afterward, it is cooled for the plastic to solidify around the insert. On ejection, the insert is encapsulated in the plastic part.
At First art, insert molding can be applied to prefabricated parts made from metal, ceramic, and other non-plastic materials. Our insert molding services are diverse, lending high aesthetics and tactile focus for better end-part use. Designers and product developers can take advantage of our material range to make parts with improved ergonomics and durability. Examples of insert molding applications are parts that house fasteners, clips or bushings, automobile air ducts, medical syringes, vacuum hose connectors, and filters containing elegant mesh inserts.
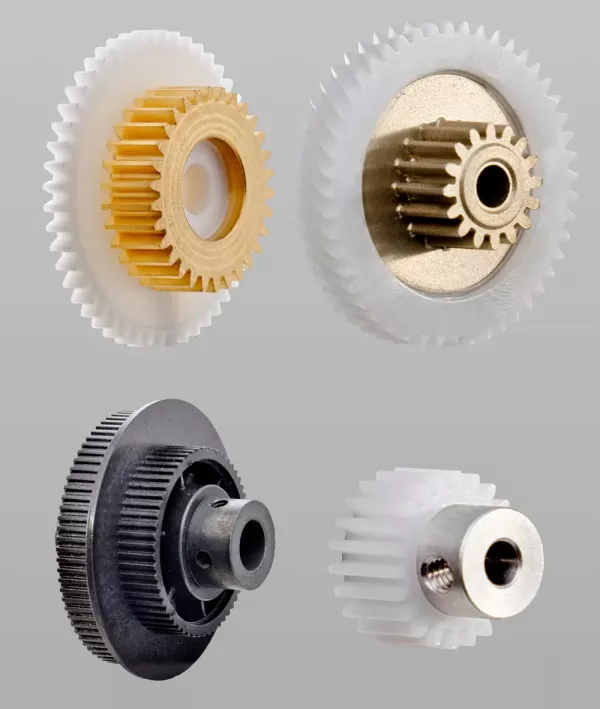
Benefits of Insert Molding
The benefits of insert molding include:
· Eliminates part assembly
· Improved part reliability
· Enhanced part strength
· Lower part costs
· Reduced part size and weight
Advantages of Overmolding & Insert Molding?
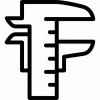
· Precision and High dimensional accuracy
Create parts with high precision and dimensional accuracy by leveraging the need for tight tolerances in plastic-over-plastic and insert molding processes.
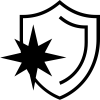
· Part durability
Overmolded parts are dust and water-tight, keeping debris and moisture out of your products for a longer lifespan. Parts with metal inserts also have improved strength and functionality, mitigating wear and tear over time.
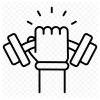
· Strength
Insert molded parts are made in a “one-shot” process capable of producing more durable parts than overmolding. Insert molded parts are also stronger than parts made from the assembly of multiple parts. The rubber-like TPUs/TPEs materials on the outer area of molded parts are also excellent for impact-absorption and shock dispersal.

· Improved functionality
Leverage multiple resin characteristics to create parts with better grip, abrasion-resistance, cosmetic appearance, electrical insulation, and more.
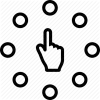
· Material diversity and options
Choose from several plastic-over-plastic, rubber-over-metal, plastic-over-metal, and rubber-over-plastic insert and over-molding material combinations.
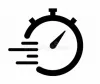
· Speed
With low-cost tooling options from aluminium, First Part can deliver insert-molded or overmolded parts in as fast as 7 days.
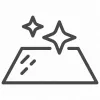
· Custom texture and finishing
Choose from a catalog of specialized finishes for plastic or rubberized insert molded or overmolded parts. We also provide a variety of customized finishes and texture to optimize your part’s ergonomics and functionality.
Overmolding & Insert Molding Applications
At First Part, our insert molding and overmolding capabilities are widely applied for:
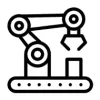
· High-functional end-part production
Overmolding and Insert molding are Plastic injection molding techniques for making mass production volumes of high-quality end parts that are functional and optimized for industry-specific ergonomic end uses.
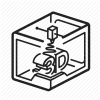
· Rapid Prototyping
Overmolding and Insert molding can be used to quickly prototype complex product concepts at affordable costs and speed.
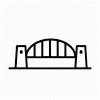
· Bridge tooling
Using aluminum tooling, insert molding, and overmolding can make small to medium-range parts at cost-efficient prices.
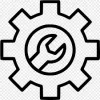
· Complex part manufacturing
Manufacture complex and composites in one-go with the “one-shot” insert molding technology. Overmolding also presents a great way to make composite plastic over plastic parts without incurring alternative multi-machining, adhesive, and assembly costs.
Material Options
Our material options are summarized under the following headings: Rigid plastic Materials, Flexible plastic materials, and Silicone Rubbers. We work with many plastic and resins as required for the application industries. In addition to our stock material options, First Part can source desired materials and provide molding with customized raw materials that will match your part’s desired application.
Rigid Plastic
· Polyphenylene sulfide (PPS)
· Polypropylene (PP)
· Acetal polyoxymethylene (POM)
· Acrylonitrile butadiene styrene (ABS)
· Glass-filled polycarbonate (PC-GF)
· High-density polyethylene (HDPE)
· Low-density polyethylene (LDPE)
· Polybutylene terephthalate (PBT)
· Thermoplastic vulcanizates (TPV)
· Polycarbonate (PC)
· Polyolefin Elastomer (POE)
· Polymethyl methacrylate (acrylic) (PMMA)
· Nylon 66 (PA66)
· Glass-filled, polyamide (PA-GF)
· Polystyrene + polyphenyl ethers (PS-PPE)
· Thermoplastic elastomer (TPE)
· Thermoplastic polyurethane (TPU)
· Custom-sourced Resins
· Customer-supplied materials
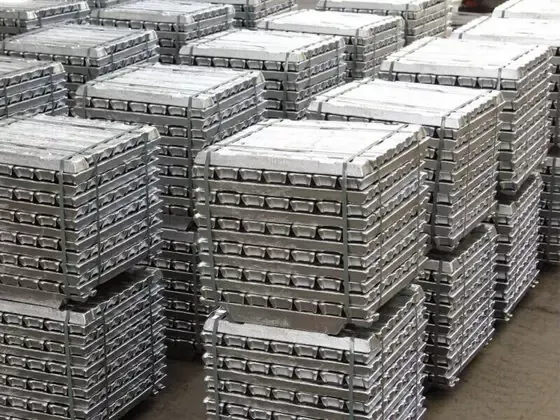
Flexible Plastic
· Low-density polyethylene (LDPE)
· ABS polycarbonate (PC-ABS)
· Polyethylene terephthalate (PET)
· Polystyrene (PS)
· Polyethylene (PE)
· Flexible polyurethane (FPU)
· PC-ABS
Synthetic Rubber
· Thermoplastic vulcanizates (TPV)
· Thermoplastic elastomer (TPE)
Silicone Rubber
· Liquid Silicone Rubber
The above materials are the most common stock material options. If your desired material is not listed above, please contact our team here. You may learn more about our other options and custom material applications by clicking here to go to our materials page.
Finishing options
Molded parts can be finished in many ways that may cover purely aesthetic finishes or offer some form of protection. Finishes should beautify and enhance the sophistication and functionality of any part. At First Part, our Injection-molded parts may be finished in any of the following options:
· As manufactured
Also dubbed “As machined,” the part will be as molded with tool marks remaining visible.This finish is suitable for parts that don’t have any cosmetic emphasis or hidden industrial components.
· Bead blasting
Bead blasting is used to even and create a uniform surface finished on machined parts.
· Pad printing
Pad printing is used as a decorative technology to transfer ink marking, logos, or texts from a pad unto the part.
· Etching
Etching is a method of inscribing a pattern, marking, or text on a molded part’s surface.
· Textured finish
The molded part is leveled with fine stone powder before being sandblasted to obtain a textured surface appearance. Suitable for finishing parts that favor a dull or satin surface finish.
· Laser finishing
The use of laser beams to etch, engrave or inscribe graphics, texts, logos or markings on a molded part.
· Semi-Glossy
Semi-glossy parts have a low amount of shininess and gloss achieved by smoothing with a fine-grit sandpaper.
· Glossy
Glossy finishes are used for achieving mirror-like and smooth finishes in molded parts. The part is smoothed and polished with a diamond buff. These parts have the smoothest surface finish relative to other finishing options.
· Matte
Matte finishes are suitable when trying to remove machining marks from mold parts without overdoing the visual appearance. The mold is smoothed with the aid of fine stone powder. Matte finishes are used on diecast, or thermoset injection molded parts.
· Custom
Choose from an array of custom finishing that is unique or a combination of some standard finishes.
Can’t find the desired finish? Click here to go to our finishing page and learn more about our array of finishing options in detail. We also offer custom finishing touches to help you achieve the desired finish or finishes for various parts.
Why Choose Us
With over ten years’ experience in Injection Molding, Insert molding, and Overmolding services, First Part is one of the best prototyping and Injection molding manufacturers in China. Here’s why:
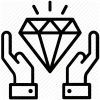
Quality and Reliability
First Part is dedicated to meeting high quality standards, delivering part on time with precision, accuracy and reliability. We follow strict quality control systems to ensure that only the best parts are delivered.
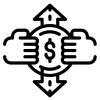
Cost-effectiveness and Turnaround
Our services ensure cost-effectiveness and quick turnarounds for low-volume and mass manufacturing. Through budget and design optimization, First Part can make your past at competitive market rates.
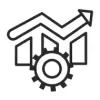
Capacity and Network
Excellent in-house capacity and capabilities, guaranteeing that your parts are made from top quality from start to finish. Enjoy non-disclosure agreements and take advantage of our network of over 20 CNC machining centres to manufacture parts home and abroad.
FAQs – Aluminum Extrusions
1. What materials are suitable for Overmolding and Insert-molding?
Depending on the application, insert molding and overmolding can be used with substrates and inserts like: ABS, Metals, PEEK, Acrylic Thermoplastics, Nylon, TPUs, Liquid silicone rubber (LSR), HDPE, TPVs, TPEs and TPRs.
Our engineers are available to help with material selection.
The general rule of thumb is to ensure the first part is made of a heat-resistant material. Also, ensure that the preferred materials for the operation do not react.
2. How quick can Overmolded or Insert molded part be made?
Before any injection molding operation can begin, the mold tooling must first be made. Depending on the part geometry and volume of parts, a low-cost aluminum tool or standard steel tool may be made. Once tooling is completed, overmolded or insert molded parts can be made and delivered in as fast as xx hours.

3. Why should I use overmolding or Insert-molding?
Overmolding and Insert molding are cost-efficient methods of increasing the functionality and performance of high-quality injection molded parts. Both processes reduce the part production time, eliminate part assembly or adhesive uses, and convey strength, impact resistance, grip, abrasion-resistance, electrical insulation, and reduced part weight to any end-use part.
4. When should I choose overmolding or insert-molding
Overmolding is suitable for plastic-over-plastic applications, while insert molding is plastic over other materials. Choosing which process is best for your part depends on whether your piece has a non-plastic component. If it does, then insert molding is the solution; if it doesn’t, over-molding is the right approach.
Request A Quote
Ready to get started? Contact us with details of your project to take advantage of our automated electronic quoting service, design verification process and excellent customer feedback program. With an extensive amount of finishing options to compliment a wide range of material types, over 100 CNC machining centres and deeply-rooted industry experience, Firstpart is always willing to collaborate and deliver functional end-use parts with quality you can trust every time.
Click here to get in touch with us and get a free quote now!